根據國際機器人聯盟(IFR)最新統計全球工業機器人市場需求在2014年開始倍增,於2016年將達到29萬部;並預估全球工業型機器人2017~2019年將以平均成長率每年13%以上快速成長,銷售台數約140萬部,而目前導入工業型機器人的前3大產業依序為:汽車、電機/電子、機械金屬。
服務型機器人則以專業應用(Professional usage robots)居多,需求量在2015年成長25%,約達到4萬1,060台;又以製造、批發零售業用的物流機器人(logistic systems)與無人搬運車(AGV)成長50%,占比達到62%最大,其次是國防、農牧等產業。
而回顧工研院在工業、服務型機器人領域發展,2005~2010年主要聚焦於服務型機種;到了2010年全力開發各款工業多關節型機器人,並從2015年開始針對CPS虛實整合應用等需求開發軟體,在2017年陸續推出輕量化、模組化機器人及關鍵零組件。
產研合造開發平台 橫跨工業及服務型領域
尤其到了近年來,隨著人類與機器人協作已成為製造業投入工業4.0時代後的重要趨勢,如何將協作型機器人(cobots)做得更精巧又簡易操作,儼然已形成機器人及零組件製造廠商的共同挑戰,工研院也在今(2017)年台灣機器人與智慧自動化展期間,率先發表與和椿科技共同開發出的驅控整合關節模組及應用技術。
工研院機械與系統研究所所長胡竹生也在成果發表會上致詞時表示,因應未來智慧機器人應用越來越豐富多元,個別製造廠商必須先行合力打造開發平台,始能與國際大廠競逐未來機器人產業的美好願景。工研院於今年台北國際自動化大展期間舉辦技術發表會,則希望能藉此引進業者合作,共同打造跨足多個應用領域平台。
投入智慧機器人模組化 整合零組件為成敗關鍵
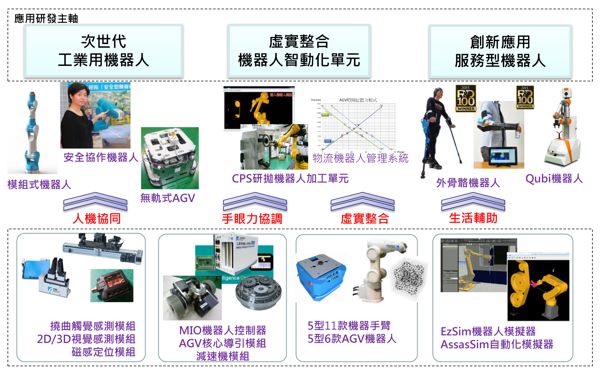
圖1 : 目前工研院所架構智慧機器人的技術平台(OISP),由零組件扮演成敗關鍵,並依序衍生出3大應用主軸,建立不同核心技術模組。(資料來源:工研院) |
|
工研院機械與系統研究所組長游鴻修進一步分析,目前工研院所架構智慧機器人的技術平台(OISP),已由零組件扮演成敗關鍵,並依序衍生出3大應用主軸:
1. 次世代人機協同的工業機器人,係自2015年推出安全協作型機器人之後,在2017年再推出模組化機種,以符合輕量、靈活等應用需求;AGV也逐步從有軌演進為無軌式設計,並嘗試解決從AC轉換為DC電源的問題,兩者還能再組合成Mobile Robot自主移動型機器人。
2. 虛實整合機器人智動化單元,分為物流機器人管理系統、CPS研拋機器人加工單元,係透過虛實整合機器人周邊軟硬體應用及手眼力協調功能,以解決不同產業問題。
3. 創新應用服務型機器人,則有外骨骼機器人、Qubi機器人等,主要用於生活輔助。
進而建立不同核心技術模組(TBB, technology building Block),包含:撓曲觸覺、2D/3D視覺感測與磁感定位模組,以及MIO控制器、AGV核心導引模組等,目前共組成5型11款工業機器人、6款AGV機器人,還可搭配EzSim研磨拋光和Assas Sim產線自動化模擬器。
整合驅控模組 提升馬達減速機競爭力
值得一提的是,拜現今Universal Robots帶動分散式控制興起、工業通訊網路技術越來越發達之賜,已形成協作型多關節機器人基礎。如工研院今年在會場展示的最新6合1驅控整合伺服系統模組,便強調經過高度機電整合完成後,有別於傳統機器人的伺服系統。不必自行選用單一控制器、伺服馬達及編碼器、驅動器、減速機等零組件,再通過電控箱內部總線整合一堆纜線,才能連接控制與驅動電路的硬體I/O模組運作。反之,藉由同時設計控制、驅動電路與程式,將運動控制器、驅動器的CPU模組整合成為一體化的運動控制器後,外觀大小相當於一個馬克杯大小的「All-in-one Motor」。
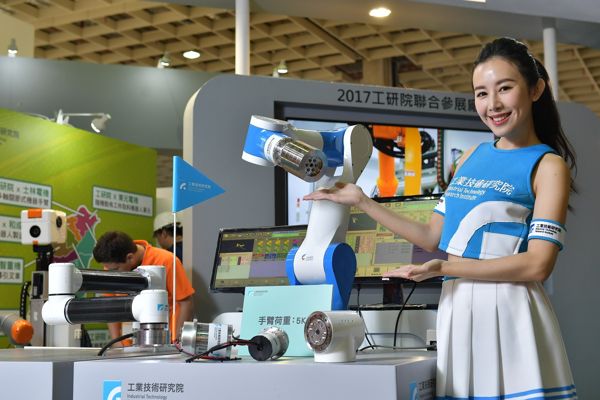
圖2 : 最新研發整合馬達、減速機、驅動電路的驅控整合關節模組,可大幅縮小機器手臂單元的空間。(圖片來源:工研院) |
|
其中包含:6軸整合AC伺服驅動器,最大功率為300W/1.2kW、位置控制解析度>17bit,且具備向量控制功能,可串連數組多軸伺服驅動模組,節省單軸驅動器複雜度;進而驅動採用DC.48V供電的永磁式無刷馬達,額定轉速3000r.p.m、功率100W/400W,可支援增量式光學/絕對式磁性編碼器介面及串列規格;還可依輸出扭力需求,以內藏式傳動模組搭配減速比約為1:100適合的減速機。
自主開發的RV減速機則突破歐日專利布局,達到背隙1arc-min、精度60arc-sec等級,與國外品牌相同精度定位和輕量化水準,介面還相容於日本Nabtesco產品。其專利設計包括將原來與輸出前蓋整合為一體的間隔柱,改為分離的傳動柱與襯套,以協助分攤輸出扭力,減少曲柄及其軸承負載,延長產品壽命;並將原斜角滾珠軸承改為滾子交錯軸承,使之更容易製造,也提高力矩剛性(Moment rigidity),相較於E型RV減重20%,還比HD減速機的剛性增加1.5倍,主要可用於工業機器人、銲接變位機、旋轉台、風力發電機等。
至於符合輕量化、體積更小需求的HD減速機,則達到減速比50~160、額定扭力4Nm~140Nm、傳動誤差<1.5arc-min規格。且因為採用高囓合率齒型設計(囓合齒數達30%),透過1~2級擺線齒輪與不同齒形設計,得以減少曲柄、軸承負載;同時考量扭矩負載與徑向彎矩作用,可符合實際場域負載情況,達到7,000~15,000hrs耐久壽命要求;並提高扭矩,減少體積和重量,更有利於生產製造的專利布局。目前主要應用於工業/服務型多軸機器人、外骨骼機器人、半導體設備等。
加上經過頻寬100MHz/1kHz的開放式全數位工業通訊網路EtherCAT介面控制,內建全數位網路伺服控制模組,支援位置/速度/轉矩控制模式,可達1ms網路通訊週期,便於匹配各式PLC、工業電腦的工業控制系統。由於全數位控制技術具有多組聯結特性,既節省單軸驅動器複雜度;工廠自動化也可透過網路傳輸,將驅動模組相關資訊傳送到遠端,實現遠端監控功能。現在包含工業機器人、線切割機、點膠機等,皆可利用控制器整合機能,導入點對點規劃路徑,以提供Total solution應用機能。
此外,因為馬達採取中空軸設計,可有效規劃配線走向,提高空間利用率;再經過精簡化的模組,只須4條纜線,即可輸出/入電源及通訊,使之整合及拆裝更方便。「讓使用者不必再像過去,須要配備一個大型電控箱隨工業機器人移動。」游鴻修說,現在使用者只要加上一顆約便當盒大小的控制器,就能輕鬆置入手提式電控箱,直接操控一台與人協同作業的輕量化6軸機器人,可說是「小空間大魔術」的具體展現。
利用模組化結構 有效改善整機與自動化配置
受惠於模組化構造而減少連接線、成本及控制箱體積,也使配線更精簡且容易維護,得以兼顧高度整合與輕量化特性,滿足各式大小及不同特性機種,皆可進行彈性客製化及自我診斷,而提高競爭力。工研院便藉此成功簡化了機器人設計,可依客戶構型要求,快速組裝完成機器人,以滿足產業多元應用場合。
同時適合做為機器人與移動平台應用,在產業容易整合機器人運動及應用控制器,目前除了投入工業生產外,還能用於機器人的技術驗證、教育訓練、DIY市場,以及特定應用領域的機器人和分散式控制系統等用途,未來還可用於輕量化機器人、輔具與AGV。
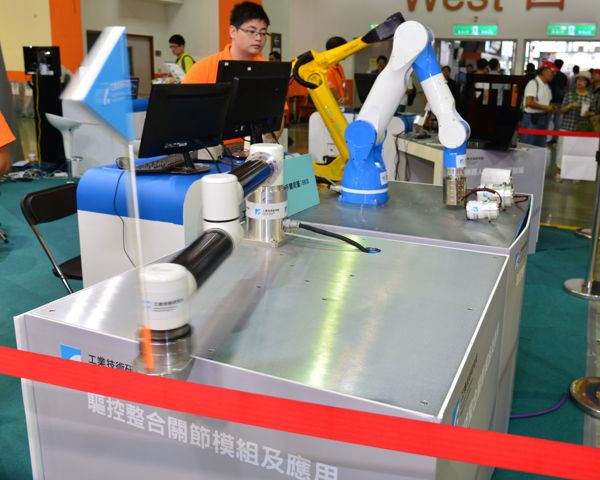
圖3 : 工研院6軸協作型、3-4軸SCARA兩款機器人依照不同構型展示其荷重能力及SCARA快速優勢。(攝影:陳念舜) |
|
機械與系統研究所副組長黃甦認為,未來驅控整合模組的價值不僅在工業機器人,還包含服務型機器人需求的輕量小型化及強力、省電需求,可組成雙臂或自主型機器人,關連到服務型機器人普及的成敗;將之縮減為馬克杯大小後,還能促進廠商為其搭建平台,創造各式機種。今年工研院也在會場發表6軸協作型、3-4軸SCARA兩款機器人,各依不同構型來展示其荷重能力及SCARA快速優勢。如L型關節模組,係將殼體直接作為手臂結構,容易組裝;I型可依雙邊支撐方式來設計手臂,具備對稱性且剛性更佳,使之抗彎矩能力大幅提升。
商機伴隨挑戰 打造多元加值平台
但他也坦言,驅控整合模組面臨的挑戰與機會並存,還包括將控制與驅動電路整合後,容易產生電磁干擾,造成訊號失真與傳輸電壓不穩;且控制器與驅動器的整體設計難度增加、體積變小導致電路散熱不易,難找到同時擁有驅動與控制技術的人才。
針對未來情境與產業效益,可透過開發多重感測與驅控技術,突破關鍵零組件仰賴進口的問題,提升台灣零組件的產業價值。經過建立智慧驅動整合模組技術,將更容易與機器人運動與應用控制器(PC-based/controller-based)整合,拓展應用到工業機器人、輔具、無人搬運車、小型伺服平台等。未來工研院還會設計多種動力規格,並建立標準規格的驅控模組,使台灣廠商能採用自主供應零組件來開發多樣化產品。