隨著數位時代的來臨,以及消費者對大尺吋、高畫質影像需求提昇的趨勢下,PDP(電漿顯示器)在競爭激烈的顯示器市場中開始嶄露頭角,而本文就其市場現況技術發展趨勢作一概略性的介紹。
市場概況
1999年各式應用市場分佈中(圖一),Color TV佔157.4百萬美元,CAGR(1999-2004年)為73%;Conference Room佔232百萬美元,CAGR為29%;Kiosks佔1.4百萬美元,CAGR為7%;Financial TerminaL佔15.7百萬美元,CAGR為57%;Public Information佔11.6百萬美元,CAGR為17%;POS/Cash Registers佔27.1百萬美元,CAGR為12%。
產值方面(圖二):1999年PDP為457百萬美元,較1998產值成長52.3%,預計2000年成長44%至661百萬美元,2005年達5,215百萬美元,而目前最大市場為Conference Room(約佔50%),成長最大者為TV市場(1999-2004的CAGR為73%)。產量方面:1999年為31.8萬台,2000年成長至37.2萬台,成長率最大者為TV市場(1999-2004的CAGR為92%)。
根據富士總研的統計,1999年全部彩色PDP出貨值佔有率依次為:FHP(43%),Pioneer(33%)、NEC(14%)、松下(9%)及其他(2%);33吋以下佔有率以FHP領先約佔71%,其餘為NEC約佔29%;33-42吋佔有率為FHP(62%)、NEC(16%)、松下(14%)、Pioneer(4%)及其他(4%);50吋以上為Pioneer(92%)、NEC(8%)。由以上的資料可知,30-50吋的市場規模較大,但相對的競爭廠商也較多,而30吋以下與50吋以上的市場則分別由FHP與Pioneer所獨佔。
技術發展趨勢
顯像原理與結構
PDP(Plasma Display Panel)電漿顯示器主要是利用氣體(惰性氣體)放電,產生UV激發管壁上的螢光粉(Phosphor)發光以取得影像,類似於日光燈發光原理,而可見光的顏色由螢光粉的種類所決定。
主要結構(圖三)包括前基板與後基板,前基板包括作為放電功能的透明電極、產生放電與降低透明電極線電阻的輔助(BUS)電極、儲存電荷之電容及驅動面板時提供璧電荷以降低驅動電壓的介電層,與在離子撞擊具保護各層材料的保護層。
就其成本結構來看,以驅動IC與玻璃所佔的比例最高,各約佔23%與22%。早期的PDP有直流(DC)與交流(AC)兩種,前者發展的廠商包括富士通、Pioneer,而後者包括松下與NHK。DC型的阻隔壁屬於格子狀,較複雜,且因電極與螢光體直接暴露在放電漿中易導致損害與劣化,因而縮短顯示器的壽命,所以目前主要以交流式結構的顯示器為主;然就投資金額來看,由於交流型PDP需使用到較多的半導體成膜工程與蝕刻方式,因此投資金額較高。
製造流程
PDP的製造流程大致分為幾個部份,可參考(圖四)與(表一):前板製程、後板製程、組合、加熱/抽氣/封入氣體、老化與電氣測試。詳細製程如下所示:
1.前玻璃基板製程
包括透明電極製作、BUS電極製作、透明介電層製作,以及保護膜製作。
a.透明電極製作:主要是以光蝕刻法、CVD的lift-off法或網印法在玻璃上形成,將ITO或SnO2層目前較常見的方式是以濺鍍法成ITO玻璃,再以濕式蝕刻製程製成所需的電極形狀,若膜厚精度與厚度不佳時會造成發光輝度不佳的現象。
b.BUS電極製作:由於透明電極電阻值過高,避免其放電時無法均勻放電,因此製作輔助(BUS)電極,利用的方法包括網印法、感光性塗膠法及蝕刻法以形成BUS電極;所使用的材料為Cr/Cu/Cr,主要的考量是利用Cu的高導電性與Cr的抗氧化性與抗腐蝕性以防止斷線的情形發生。其中網印法雖可較節省材料,但解析度受限制;濕式蝕刻法的精密度較高但是所浪費的材料較多。
c.介電層製作:利用網印法、塗佈法與貼層法形成介電層,主要材料是玻璃粉,目前較常用的方式是以網印法形成多層的介電層,要求平整度高且不能產生氣泡。
d.保護層的製作:主要以塗佈法(成本便宜速度快但所需的燒成溫度高)、電子束蒸鍍法(目前主要的方式)、濺鍍法(成膜品質佳但速度慢)及離子植入法(成膜速度快且均勻性佳)將MgO形成保護膜。
此外有些電漿顯示器為增加顯像品質,因此會加上黑色矩陣(black matrix)以增加對比,並加上濾光片以增加對比與色純度。
2.後玻璃的製造
a.DATA電極的製作:以感光性塗膠法、網印法、光蝕刻法、Lift_off法將Ag作成電極。
b.阻隔壁的製作:阻隔壁的製成品質良否會影響到PDP的後續良率與顯像品質,因此這是PDP廠商努力研發的重點,截至目前為止也發展出許多製成,包括:網印法(製成簡單、設備成本低,但良率提昇與精密度難控制)、噴砂法(精密度較高,為目前主要方法,但易造成粉塵與材料浪費)、真空成膜+剝離法(縮短老化與封合時間但成膜速度慢)及壓膜法(製成簡單但平整度不易控制)將低融點玻璃與氧化鋁製成阻隔壁,作為阻隔壁的材料要防止相鄰CELL放電所產生的cross talk現象,以及能支撐前玻璃基板的強度,要求的特性為:所有阻隔壁的高度均需一致,以防止各CELL中的氣體互相流通、避免有開放性氣孔存在,而改變混合氣體的比例。
c.螢光層的製作:螢光層主要作為發光顯像的材料,製程包括:網印法、感光性漿料法及乾膜壓合;目前以印刷法為主,螢光粉的塗佈需注意到均勻性與相鄰兩CELL間不可以有混色的情形發生。
3.面板工程製程
面板工程乃是將前玻璃與後玻璃基板裝配,然後進行密封、排氣、封入氣體、老化與檢查等製作過程。
封合的目的是經由封合材料將前後兩塊基板貼合,接著進行排氣與灌入氣體的過程,排氣與灌入氣體均藉由具排氣孔的管子進行,在排出雜氣並灌入惰性氣體後,將管子切斷、溶解封止;接著為老化的過程,此製程最主要的目的在使各個放電空間之發光特性穩定。完成老化的過程之後,主要的面板工程大致已完成,另外為了降低面板的反射光及減少EMI的干擾,會在PDP面板外再加上一片壓克力或玻璃做的外板。
最後的製程為驅動電路與面板支持體的安裝,以現在VGA級的PDP面板約需使用到38個驅動IC,若是XGA則需使用到68顆,其所佔之成本比重相當大,而影響驅動方式設計的因素包括:氣體放電特性、發光效率、對比及耗電量等。隨著未來PDP的大尺吋化,保持畫面亮度的均勻性也是必須克服的問題,在構裝方式方面,預計未來驅動IC並非一顆顆安裝,而是朝模組的方式進行,最後面板支撐體必須具有剛性、散熱佳的特性。
增加輝度的方法包括提升螢光體的發光效率、提高封入氣體的壓力、放電空間的擴大及提高電壓;增加對比包括有效應用color filter、製作black matrix;減低電力消耗包括提升螢光體的發光效率、降低driver IC電壓;增長壽命包括電極材料與螢光體的改善、採用3電極放電、製作保護層(MgO);電磁波的對策採用noise-cut filter,對於如何提高顯像品質,各廠商也提出不同的技術,分述如下:
◎富士通:隨著解析度的上昇,單位面積內的CELL(最小的發光單位,一般以RGB三個CELL構成一個畫素)數會隨之增加,相對的放電空間也會縮小,亮度隨之下降,富士通為改善此種現象而發明Alis(Alternate Lighting of Surfaces)技術,以同時解決亮度與解析度的問題。其原理乃是取消為確保放電的獨立性而設置「非發光區」,方法即在後基板塗佈螢光粉與充填放電用氣體,使原本的「非發光區」亦變成「發光區」,使發光方式由「同列閃爍發光」變成「異列閃爍交互發光」呈現,整體來說面板結構並不需有太多的改變,只需變更電極的距離,藉由此種技術亮度更可從原本的250-300cd/m2提昇至500cd/m2。
◎PIONEER:採用新結構的CELL。一般傳統區隔CELL構造的阻隔壁為直線狀,因為上下CELL間並未設置阻隔壁,因此會彼此干擾,造成垂直方向對比不佳,以及電極的遮光效果造成發光效率下降等缺點;PIONEER則採用格狀的阻隔壁(WAFFLE結構)來改善上述的缺點,使垂直水平方向的對比皆能提昇,加上水平方向亦設置阻隔壁,因此可塗佈螢光粉的面積加大,而經由以上技術可提昇約20%的發光效率。
◎松下:採用「非對稱CELL結構面板」,並加強螢光粉的材質,此舉不僅能均衡RGB的發光情形,更能表現純白的顏色。
4.其他大型顯示技術--PALC(Plasma Addressed Liquid Crystal Display)
日本SONY、Sharp以及荷蘭Philips公司,在1997年七月合資生產40吋的PALC電漿定址液晶顯示器。PALC顯示技術是在1991年由美國太克公司與日本SONY共同提出的新顯示技術,後來這項專利權交由SONY使用。
目前研發分工的內容為SONY從事PALC技術開發,Sharp從事ASM(Axially Symmeric aligned Micro Cell Mode)的技術開發,而Philips則進行產品高精細化的改良。由於要在40吋玻璃基板上長出薄膜電晶體並不是一件容易的事情,而且製作的成本也會相當昂貴,於是採用電漿顯示器的氣體放電原理來取代液晶面板每個畫素的電晶體驅動元件。
PALC電漿定址液晶顯示器的面板結構如(圖五)所示,在50μm的介電質玻璃基板與背玻璃基板中間充入氦氣或是氖氣的鈍性氣體,當陰極電極加上-350V的直流負電壓,而陽極電極為0V時,鈍性氣體會發生高電場氣體放電的效果,並且會在介電質玻璃基板上產生壁電荷,而這層壁電荷就好比是一層虛擬電極。虛擬電荷會和ITO玻璃基板的透明電極產生電壓差,於是灌入於介電質玻璃基板與前ITO玻璃基板的液晶材料將因為電壓差所產生的電場而引發液晶分子排列方向偏轉,進而使通過的入射光的極化方向也發生偏轉作用。電漿定址液晶顯示器也是採用上下兩片偏極板來產生顯像灰階效果,同時也是利用彩色濾光片來產生全彩色的顯像。PALC電漿定址液晶顯示器跟一般的液晶顯示器一樣,也是必須使用背光源。
整體來說,PALC電漿定址液晶顯示器的背玻璃基板製作過程與PDP電漿顯示器相同,採用隔牆方式區分每一個掃瞄線,利用氣體放電的電荷當作驅動電荷。而前玻璃基板與液晶面板製作過程與一般的液晶顯示器後段製程相同,包括灌入高分子液晶材料、封裝、貼上含有彩色濾光片與透明電極的前玻璃基板。
目前這三家公司所展示的產品是42吋寬螢幕面板,解析度為854×480,面板亮度為400 cd/m2,對比值為100:1,觀賞視場角是140度。據SONY公司表示,目前這款PALC電漿定址液晶顯示器尚在試產階段,一旦顯示器面板的觀賞視場角可以達到160度時,該公司就會開始進行量產並推出上市。
(表二)為SONY公司PALC電漿定址液晶顯示器與AC型PDP電漿顯示器特性比較表,在觀賞視場角度與影像對比率方面,PALC技術顯然比PDP電漿顯示器來的差些。
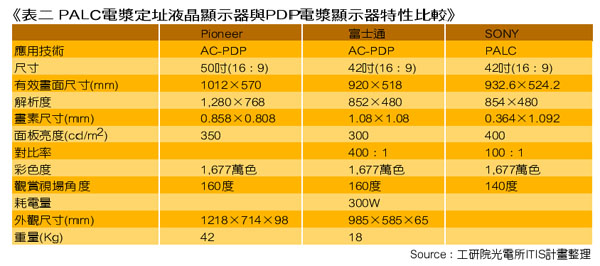
《表二 PALC電漿定址液晶顯示器與PDP電漿顯示器特性比較》 |
|
結語
整體來說,PDP技術研發的目的有兩個:提高產品品質與降低製造成本,也唯有如此才能提供更高功能價格比的PDP,以便在競爭日趨激烈的顯示器中佔有一席之地。