受到當今全球疫情對於產業供應鏈的衝擊,不僅改變製造業的營運模式,也加速傳產金屬加工業發展智慧製造、AI與大數據分析等應用,力求朝向工業4.0數位化轉型。但長期深耕企業數位轉型服務的東捷資訊特別呼籲金屬加工業,數位化轉型應該循序漸進,首要之務是將人員、機台設備、物料產品、生產方法與生產現場環境等5大要素進行升級更新,使工廠逐步從「自動化」走向「智能化」。
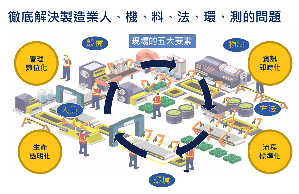 |
東捷資訊自行研發的智慧製造核心MES,協助金屬加工業達成數位化管理、資訊即時、生產透明與流程標準化等目標。 |
尤其隨著目前雲端運算、大數據、機器學習、AIoT等新興科技在後疫時期加速發展,各行各業進行數位轉型已是不可逆趨勢,根據TrendForce 研究報告顯示,預期到2025年,全球智慧製造市場規模可望達4,500億美元,年複合成長率為10.5%。傳統金屬加工業面對勞動力不足及疫情衝擊帶來的全球供應鏈改變,在營運上將面臨:
1. 品質:無法掌握生產即時進度與生產品質情況;
2. 交期:訂單交期縮短;急單、插單或客製化訂單情況增加;
3. 成本:供應鏈管理時效縮短與作業員短缺,人力與最少訂購量(MOQ)成本增加等挑戰,
因此,業者唯有調整傳統生產模式,積極數位轉型,邁向智慧製造才能持續保有競爭優勢,且在導入過程中,人員、設備、物料、生產或環安問題須同步進行優化,不可偏廢;作業管理層、企業管理層、企業營運層的IT服務更是缺一不可。
由東捷專業顧問團隊提供的製造執行系統(MES)與顧問服務,則已藉協助多家金屬加工業者導入MES的成功經驗,深度了解客戶所面臨的痛點及掌握製造轉型關鍵成功因素,將足以滿足該產業製程與關鍵系統需求,達成數位化管理、資訊即時、生產透明與流程標準化等目標;進而協助業者整合新舊系統、數位化轉型及接軌國際,有效提升管理、生產效能和競爭力。
東捷資訊服務營運副總經理劉新正表示:「東捷不僅擁有多年豐富的製造業產業Know How,更具有從OT(操作科技)、IT(資訊科技)到DT(數據科技)的完整解決方案,近日更完成國際馬達大廠供應鏈廠商之一的矽鋼片沖壓廠產線設備稼動率監視與現場看板管理。讓客戶可以即時掌握現場設備運作與產量的決策數據,提高生產力與改善設備稼動率;下階段即可連接MES,以蒐集訂單與生產過程的人、機、料、法、環等數據,提高智慧工廠管理效率。」
舉例來說,成立於2013年的金上晉科技公司,以不銹鋼金屬製品結合環保的PVD真空離子表面處理領先市場,並在海內外分設多個廠區。但近年來面對客制化訂單高度需求,使得營運管理的風險增加;再加上原始生產數據僅有統計報表,無法進行追溯管理。在2020年東捷協助導入MES之後,便有效幫助了金上晉即時掌握生產進度與溯源管理,提升產品品質與服務效率,加速其從傳統金屬製品產業轉型發展為高科技技術的領頭羊。
金上晉科技公司協理蔡昌儒指出:「在導入MES系統之後,各生產單位主管得以隨時掌控每張工單目前生產狀況及物料流向,配合對應產出報表,可以精確掌控相關生產效率和良率;在生產運作流程上,也讓線上人員直接遵循著生產作業藍圖運行,避免了很多人為的流程失誤,且容易分析出原因,並配合做出適當的處置。」
看準金屬加工業強化數位轉型下對於生產進度精準追蹤等需求,東捷以熟知機電製造業的專業輔導顧問為基礎,現已協助多家金屬加工業客戶導入MES,以針對主要工藝技術製程,提供了完整的解決方案,包括:針對金屬成型多量多樣的生產特性,提供鑄造、鍛造、沖壓、裁切等批量方式的派工與報工;如車削、銑削等金屬切削加工製程等自動化設備,提供開放API串接設備資料,並針對部份需進行外包製程,提供了外包報工等功能,以協助企業即時掌握生產進度與溯源管理,提升產品品質與服務效率。此外,報表查詢功能,更可協助使用者追蹤完整產品的履歷,實現管理數位化、流程標準化與生產資訊即時、透明化的智慧工廠。