现阶段的射出成型设备业者正透过大数据、物联网和智慧系统等创新技术,来提高对能源使用的可见性和控制力。更进一步的还会以简单而有效的方式进行创新。
射出成型是生产大体积聚合物零组件最常用的制程技术之一,应用也愈来愈广泛,2020年全球塑胶市场规模为5797亿美元,2021年为5900 亿美元,预计2022年至2030年将以3.7%的复合年增长率增长。在市场不断成长的背景下,另一方面所带来的就是提高品质与生产成本的竞争。
期??获得高品质的射出成型产品,必须使用最好的设备和制程叁数,这些叁数并不总是很容易定义,传统射出成型技术人员,几??都是根据自己的经验,再加上反复试验方法来获得现场经验。
虽然利用射出成型所生产的产品外观的几??都一样,但是由於制造过程是动态性,因此叁数也会不断的变化,每个过程都存在生产出缺陷零件的可能性,这种情况就会带来不可预测的成本。在塑胶射出成型中,最常见的缺陷是:未填充、毛刺、烧痕、短射、翘曲和流线。为了防止这种潜在的负面事件,如果能够使用一种可透过制程特徵的变化,来监测和预测有缺陷零件的生产方法,就会为生产线带来更多的生产效益。
今天的工业4.0时代,很大程度上依赖於数据驱动的精确性,利用人工智慧(AI)及这些数据来提高设备的性能,已经发挥出越来越大的作用。
制造业中的人工智慧包括一系列技术,使设备能够以模仿人类的智慧来执行操作。而机器学习和自然语言处理,更可帮助设备接近人类的学习、判断和解决问题的能力。因此增强数据资料的效率,将会使的整体生产作业流程更快、更具成本效益。
应用实例包括机器人系统的自动程式设计,有针对性的故障补救,以及带有'智慧'影像处理的备件系统(Spare Parts System)。因此,接下来的注塑成型设备将一步步变得更加智慧,以确保机器能不断学习,保持自身稳定,甚至可以在未来进行自我最隹化(图1)。
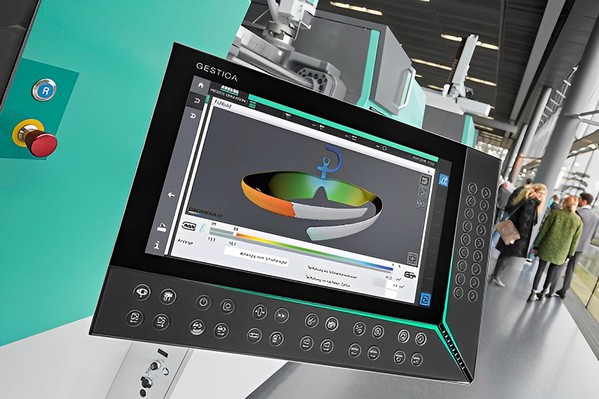
图1 : 未来的一个大问题是确保生产设备不仅保持自身稳定,而且还能自我最隹化。(source:ARBURG) |
|
作业转向自动化 人工智慧越来越重要
人工智慧在机械工程中变得越来越重要,将熔融塑胶注入模具并冷却,以形成所需形状的射出成型制程正变得越来越自动化、高效和精确。这为业者节省了大量成本,为消费者提高了产品品质。今天射出成型方法被广泛用於生产消费性产品和汽车零件。更进一步的,如今整体产业的趋势已经朝向「生产数量规模越来越小,产品生命周期也越来越短」的型态出现演变,因此更需要高效灵活地自动化射出成型的生产制程。
人工智慧影响射出成型的主要方式之一,是透过使用智慧感测器。这些感测器在收集成型相关变数的资料,如温度、压力和流速。再由人工智慧演算法进行分析所收集到的资料然,来确定生产模式和可能发生潜在问题。例如,如果熔融塑胶的温度过高,系统就可以提醒操作员并调整制程,防止最终产品出现无可弥补的缺陷。
而另一种影响生产的方式是利用预测性维护。在整合感测器的资料後,来确定模具何时可能磨损或发生故障,就可以在模具发生故障之前安排维护,从而节省时间和金钱。
因此人工智慧的导入,为传统塑胶加工制程带来了过去所难以达到的优势性,包括了:
预测性维护:可预测设备何时可能发生故障,并在任何故障之前安排维护,进而减少停机时间,以及延长设备的寿命。
品质控制:透过人工智慧监测零件的品质,并根据需要调整叁数,来确保品质稳定。
制程优化:利用分析设备的数据资料来优化射出成型过程,并且调整制程,进而提高效率,减少浪费。
材料优化:通过减少使用的材料和尽量减少浪费来节约成本。
机器学习:训练机器学习和适应新的生产过程,达到更有效和高速的生产周期。
对注射过程影响最大的变量,包括熔体温度、塑化时间、最大压力、模具壁温和注射时间。因此进行机器学习时,就需要经常选择温度、注射时间和循环时间作为重要因素,同时还必须监控喷嘴和缓冲垫之前的循环时间、塑化时间、射出时间、Barrel温度。
利用智慧设备来提升生产效率的研究
利用机器学习来有效提升生产效率方面,葡萄牙雷利亚理工学院的Bruno Silva研究团队,曾经做过了一次完整的数据统计和分析。而这些所有的数据,是在葡萄牙一家拥有多种制程的塑胶射出成型业者-Vipex的真实场景中获得的。
此次的研究中,使用了Vipex工厂内的三款机台,分别是TedericTD850、Negri BossiNB400和Nissei ASB。三种机台各自的工作方式不同,具有不同的生产周期持续时间、模穴数量和同一时期生产的产品数量,这些差异都会影响到指标的度量标准。
因此,Bruno Silva就个别分析这三种机台,其性能指标分析分级机性能的指标是整体设备效率(OEE)、首次合格率(FPY)、次品数量和机器停机时间。当然还必须考虑其他指标,但因为这次所进行实验测试,有许多客观因素地限制,而无法计算这些指标。
因为着作权的关系,在此只能简短地叙述出研究的结果,如果有兴趣的读者,可以寻找Bruno Silva研究团队的研究论文《Enhance the Injection Molding Quality Prediction with Artificial Intelligence to Reach Zero-Defect Manufacturing》,这篇里面有详细说明研究的方法和理论基础。
以下就针对研究结果做一说明。
目标设备:TedericTD850
TedericTD850的生产周期为 77.1 秒,只有一个模穴,每周工作5天,每周共生产5,603个零件。在没有任何分类器(Classification)的情况下,原始的OEE为 77.4%,停机时间为15.1%,FPY为89.5%,共有588个不良品。而在所有这 588 个缺陷产品中,120个是无法避免的,例如机器清洁停止等。
因此可以针对这468个不良品再深入研究,由於分类器的准确率约为92%,因此在这468次不良品中约有37次无法正确预测,除此之外,431个不良品都可以准确地被判断出来,以及获得相关数据。此外,停机的时间也降低到了6.52%(图2)。
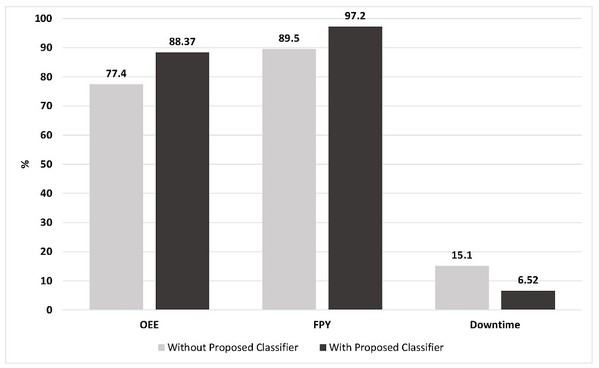
图2 : 使用和不使用机器学习分类器的TedericTD850机器指标。(source:葡萄牙雷利亚理工学院) |
|
Negri BossiNB400
Negri BossiNB400的生产周期约为47.8秒,它有8个模穴,这意味着它每个周期会生产出8个零件。由於模穴数量较多,这台设备生产的产品会比其他设备来得多。监於此基础,加上它每周工作五天,预估这台设备每周生产大约72,301件产品。所有生产的产品中约有10.5%存在缺陷。经过统计在生产过程中,总共出现了7,592个不良品。
在这7,592个不良品,其中有720个是不可避免的。同样使用使用准确率约为92%的分类器後,无法预测出的不良品大约有550个。
由此得出结论,在生产过程中可能发生的7,592个不良品中,大约有6,322个可以成功被妥善处理,而停机率也大幅度的下滑到5.59%(图3)。
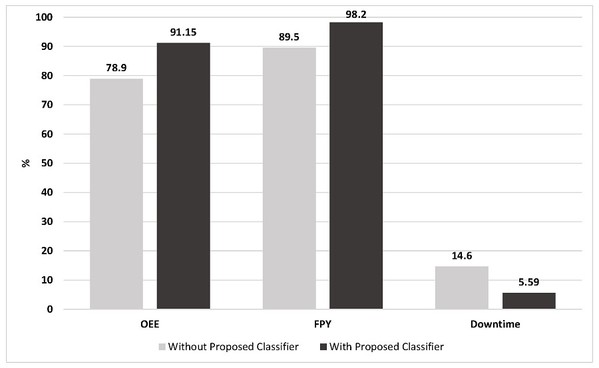
图3 : 使用和不使用机器学习分类器的Negri BossiNB400机器指标。(source:葡萄牙雷利亚理工学院) |
|
Nissei ASB
Nissei ASB的生产周期持续时间为19.2秒,内部有两个模穴,因此在每周工作五天之後,总共可生产45,000个产品。和前两台设备比对之下,Nissei ASB的生产效能非常稳定和高速,只有大约1.6%的产品有缺陷,也就是说每周只会出现720个不良品。在这720个不良品,有90个是生产过程中无法避免的。
分类器的准确率约为98.96%,这意味着只会有7个不良品无法被正确预测。扣除所有不可避免的不良品,大约有623个不良品是可以成功避免的。而而停机率更是低至1.04%(图4)。
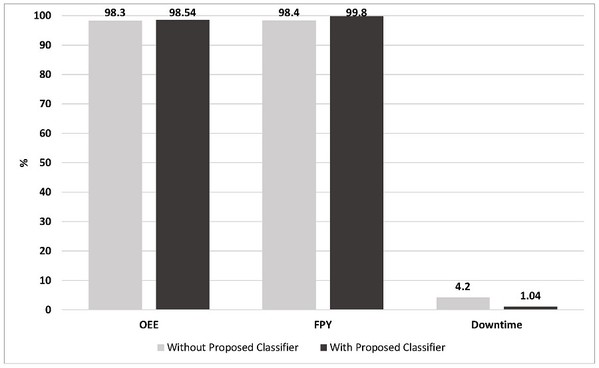
图4 : 使用和不使用机器学习分类器的Nissei ASB机器指标。(source:葡萄牙雷利亚理工学院) |
|
机器学习可大幅减少停机时间
总而言之,经过这次Bruno Silva团队的研究,可以发现到在制造过程中,导入了机器学习分类器可以产生了积极且重大影响。与生产的零件总数相比,Tederic和Negri Bossi的不良品要多得多,这导致性能指标给出的评价较低。另一方面,Nissei ASB 机器更稳定,与生产的总数相比,不良品非常少,因此一开始就获得了良好的评价。
可以确定,对於Negri Bossi来说,OEE 最多可以增加12.25%,而Tederic可以增加 10.97%。对於这些设备,FPY即好产品占总产品的比率,也有显着增加。不良品数量和设备停机时间也显着减少。
停机时间的减少是由於能够预测所生产零件的品质问题,甚至可以在生产过程中,在出现不合格零件之前就可以对其进行干预。而Nissei ASB本身的生产稳定度就非常高,因此获得的成效并不如另外两部设备高,
从这次实验可以看出,对於生产效能来说,机器学习分类器的导入确实会产生了正面影响。看到的最大影响是设备的停机时间。从指标结果来看,在制程中导入分类器前後,很容易得出分类器在流程效率已经是很差的情况下,对流程的影响更大。当流程已经有很好的表现时,导入机器学习分类器就不会产生那麽大的影响。
面对节能减碳下的射出成型生产技术挑战
除了如何透过先进的科技,让传统塑胶射出成型制程获得前所未有的生产效益之外,在节能减碳意识高涨的今天,射出成型是否环保、要如何减少能源消耗,也就成了另一个重大的问题。
射出成型整面临两个主要的环境挑战生产效率和材料的影响。射出成型技术发明於1800年代後期,最初的生产过程并未考虑到对环境的影响。因此,许多业者也未曾考虑过这一问题,但环保意识抬头下,这些业者也正面临环保团体的群起批评。
具体而言,制造过程中使用的能源量、从化石燃料中制造原生塑胶的影响,以及将抛弃式产品弃置到垃圾掩埋场的背景下,射出成型产业也贡献了世界20%的碳排放量。这也就是射出成型产业正面临的主要挑战。
由液压驱动朝向电机式系统发展
直到20世纪末,射出成型机都是由液压驱动的。除了使用石油外,液压机在生产过程中还浪费了大量能源。相比之下,电机式系统能透过叁数得到严格控制,从而使高效化生产过程和降低对能源的使用(图5)。
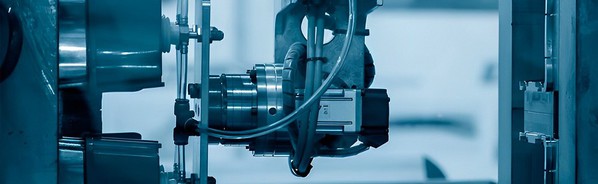
图5 : 透过将旧设备升级为电动系统,业者可以在生产过程中节省高达60%的能源。(source:Essentra Components) |
|
根据统计,如果将旧设备升级为电动式,业者可以在生产过程中节省高达60%的能源。尽管这对工厂来说是一项重大的前期投资,这一改变不仅会减少碳排放,还会减少电费和运营成本。
另一方面,射出成型使用高耗能来制造塑胶零件。这是因为制程中需要将聚合物加热到非常高的温度,并在极压下将其注入模具中。并且根据所使用的原料和模具的类型,需要使用不同的温度和压力。
但透过今天的人工智慧技术,可以大幅度的将叁数最隹化,而这种最隹化也就意味着不会浪费过多不必要的能源,尽可能地提高效率。同时与电机式系统相结合下,更可以严格控制制程叁数,获得更高品质的产品和更好的能效。
因此现阶段的射出成型设备业者正透过大数据、物联网(IoT)和智慧系统等创新技术,来提高对能源使用的可见性和控制力。更进一步的还会以简单而有效的方式进行创新,例如Essentra Components在设备的挤压机筒上使用隔热套,如此一来可减少了15%能源使用量,从而显着的降低碳排放量。
结论
总之,射出成型产业是制造业中一个充满活力且不断发展的行业。包括技术、材料、设计、市场和管理等方面的最新趋势正在源源不断的注入这个产业和生产设备,来提高射出成型产业的可持续性、高效率和创新性。
因此,紧跟这些趋势并相应地调整其流程和产品的业者将处於有利地位,相信可以在这个竞争激烈且瞬息万变的行业中蓬勃发展。
叁考资料
[1]葡萄牙雷利亚理工学院 Bruno Silva研究团队,Enhance the Injection Molding Quality Prediction with Artificial Intelligence to Reach Zero-Defect Manufacturing.