這幾年來,3D列印這個詞彙經常可在不同的領域中被發現。儘管看法兩極、評價不一,然而3D列印對於小量生產或原型設計存在著重要的價值,這是不容忽略的事實。而現在,市場也一直在試著找出更適合3D列印的應用領域,直接數位製造(DDM)似乎是個不錯的起跑點。
當3D列印遇上了直接製造,似乎也為3D列印打開了一扇全新的商機之門。在各個不同領域,都有3D列印直接製造的實際案例,本文就將嚴選包括交通、醫療、文創等不同領域的3D列印應用,看看兩者的結合,會擦出怎樣的新火光。
自行車列印一氣呵成
3D列印技術十分適合用於交通工具的列印,目前已有採用3D列印的汽車問世。但請不要誤會,3D列印的車輛並不是整車列印,畢竟車子的引擎、晶片等構造以目前的技術來說,仍是無法直接列印的。
目前最常使用到3D列印技術的部分,都還是在非關鍵零件上,例如2010年11月,美國和加拿大兩家公司成功研製出全球第一輛透過3D列印技術製造的Urbee 3D列印油電混合車,其車身外殼材料等外部組件,便都是利用3D列印所產生。
當然,這樣的方式只能用於產生車身外殼,之後還得另外組裝上底盤與引擎等部分。對於交通工具的整車列印,目前已有英國的EADS公司透過尼龍材料,打造出堅固程度等同於鋼鋁合金的Airbike自行車,且重量能輕上65%。
傳統的合金自行車組件,例如齒輪、踏板、車輪等,都屬於必須分別製造,再進行組裝的不同零件,不過Airbike在電腦設計完成之後,就可以透過3D列印來進行整車製造,所有結構包括車身、車輪、軸承等重要零件,都可以列印來完成。
其列印方式是使用積層製造(Additive Manufacturing;AM)技術,利用粉末狀材料的印表機來列印,電腦先將3D設計圖分割為許多2D圖層,再透過雷射光束來融化這些粉末材料進行列印,這些尼龍材料逐層堆疊,進而成為自行車的各個部分零件。
EADS所採用的這種積層製造技術,可讓不同的粉末材料諸如尼龍、碳、鈦、不銹鋼、鋁等,透過雷射融溶的方式進行列印,擁有非常不錯的商用前景,是可以改變現有遊戲規則的技術。
雷射能夠塑造出各種不同形狀,其優勢在於可透過低成本的生產方式,來完成複雜的設計。例如在Airbike的結構中,就具備了彈性座椅與整合軸承,這都是必須透過這種積層製造技術才有辦法做到的。
類似Airbike這樣的3D直接製造,可以依據消費者的要求進行產品設計並列印,一氣呵成的一體化設計,不僅具有客製化優勢,成本更比傳統自行車重量減輕65%,所使用的材料也僅為傳統自行車的10%,列印完成即可進行組裝使用,省去了傳統自行車人工組裝的成本。對於直接製造來說,Airbike是個十分成功的範例。
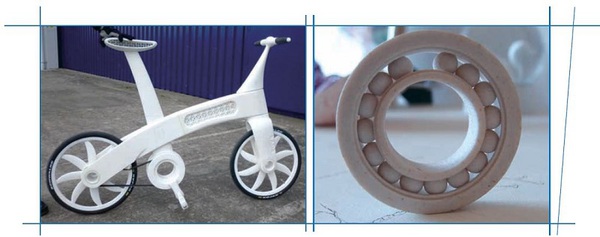
圖一 : Airbike是3D列印交通工具的成功範例,特別是軸承的部分,都能精確地列印產生。 |
|
器官組織列印 長命百歲不是夢
3D列印最適合用於客製化小量生產的用途上,這使得醫療市場也成為3D列印能盡情發揮的目標領域。畢竟每一個個人都是獨特的個體,一旦受了傷,或者需要器官再造,就能透過3D列印,直接產出每個人所需要的不同組織。
當然,不像一般冷冰冰的零件,器官必須是活的,還要能與身體其他組織共生。因此,3D生物列印可是件非同小可的事情,所列印的「產品」,也分為有功能性的器官(如腎臟、心臟等),以及修飾性的組織(如耳鼻軟骨、骨骼修補、表皮等)。
對於功能性的器官列印,不久前在TED大會上,外科醫生Anthony Atala捧出一顆3D列印腎臟的畫面,相信至今還令許多人印象深刻。事實上,要用3D列印出生物器官,原理相同,但材料肯定不同。
生物列印所使用的材料,必須是病人本身的細胞(可以是幹細胞或者自身培養的細胞),這又稱為生物墨水,作用與一般列印時的墨水材料類似。
為了列印出與原病人相同的器官外型,必須先透過電腦斷層掃瞄,將器官模版輸入電腦,然後將墨水輸出在平面材料上並固定,再將這些平面材料堆疊,待生物降解後,剩下的細胞就能成為3D的立體器官了。
事實上,3D生物列印的原理,非常類似於過去就存在的器官培養。列印器官最大的用途,當然是在於解決器官捐贈數量不足的問題,例如等待腎臟移植的病人通常都是一腎難求。以目前非常缺乏器官捐贈者的情況來看,未來透過3D生物列印,的確可以解決等不到器官導致病人死亡的問題。
用3D生物列印來製造新器官,儘管聽起來感覺像是『需要的時候印一下就有』,但當然不會這麼簡單。包括穩定的材料、細胞的取得,以及血液的供給等,都還是有待克服的難題。
相對於器官列印的高複雜度,列印修飾性的身體組織,相對簡單快速得多了。例如近期便有患者因面部殘缺,透過3D列印來製作修飾新皮膚,只需透過簡易黏著便能輕鬆重建容貌。
另外諸如耳鼻的軟骨等,也都能透過列印來還給患者一個全新的外貌。特別是例如耳朵的重建,列印時可將生物材料與具備天線的電子材料結合,讓電子耳朵還能賦予患者助聽的能力。
不久前,還有患者以鈦粉為材料,透過3D技術量身列印出專屬的新下巴,來替換掉原有的受損下巴骨,由於下巴作用為咬合食物,結構需要更高的強度,據悉整個新下巴骨共鋪了上千層的鈦金屬粉,十分費工。
此外,也有病患以3D列印技術獲得全新的顱骨,重建了自己的外貌。而牙齒與齒模,更是3D列印在醫療應用中,最大的一個市場。
事實上,3D列印的特色,本來就在於小量客製化生產,不僅適用於原型設計,而像是醫療這一類專為不同患者量身打造新組織的應用,更是3D列印能夠發揮所長的領域。當然,修飾性的身體組織列印,對於直接製造來說,將比起器官列印來得更容易實現。
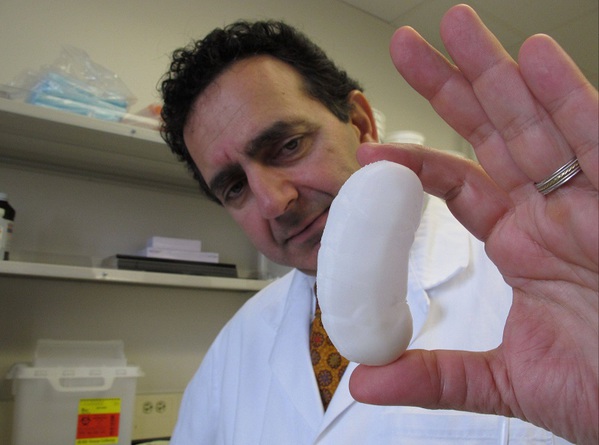
圖二 : 器官也能直接列印?圖為外科醫生Anthony Atala與手上的3D生物列印腎臟的原型。 |
|
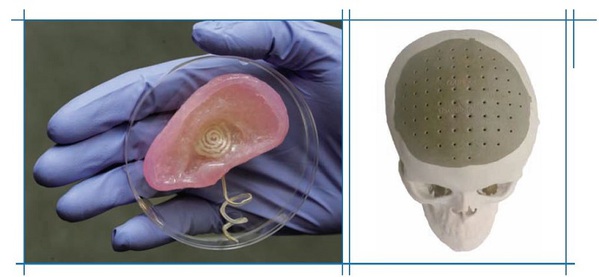
圖三 : 3D列印特別適合單一客製化的醫療市場,特別是在修飾性的身體組織列印。 |
|
迷你公仔征服消費市場
說到3D列印在消費性領域的應用,可說是包羅萬象,簡單的物品例如筆筒、收納盒、小擺飾等,都可以利用入門版的3D列印機在家裡輕鬆完成。然而這些應該都難以滿足消費者挑剔的味蕾,他們希望3D印表機可以用來完成更與眾不同的事情,例如個人化的個性公仔,便是可以利用3D列印來完成的終極任務。
目前台灣已有業者將日本Mikanbako的3D列印技術帶向台灣,透過這種技術,可以將整個真人複製成迷你版的分身公仔。當然,由於是需要製作與真人相同的公仔,前置作業便需要先進行全身3D掃瞄,包括身體與髮型,都必須分別進行掃瞄,來獲得擬真的3D人形樣貌。
當掃瞄完成,獲得全身的3D圖之後,就要開始進行後製的列印作業了。儘管台灣業者與日本合作,但後製作業卻必須回到日本進行。在進行3D樣貌圖的微調之後,影像匯入電腦便可開始進行人形的列印。
值得說明的是,人物公仔並非列印完即是成品,還需要經過初步修整、細部處理與上色等步驟,才會變得與所小版的真人一模一樣。
這樣的公仔製作,未來將非常有其消費市場的商業價值,大家都會想打造一個自己專屬的分身公仔。甚至這樣的列印技術,還能用於為寵物,以及其他物品製作縮小版的公仔。
目前每個分身公仔的定價仍偏高(25公分公仔定價約為19550元新台幣、20公分公仔約12750元新台幣),未來隨著列印技術較為普及,價格到達友善價位之後,應該會帶起一股迷你公仔的列印風潮。而迷你公仔的製作,也預計將為文創產業,帶入一股3D直接製造的新活力。
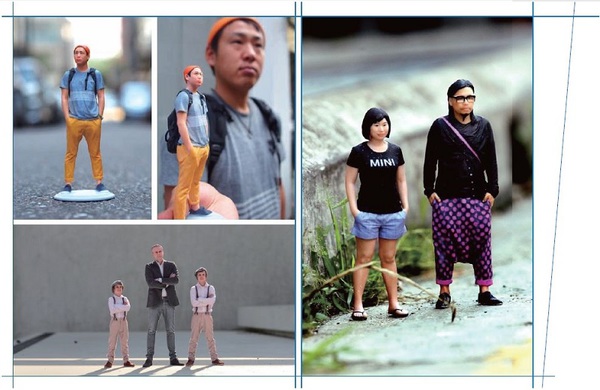
圖四 : 用3D列印做出縮小版的人形迷你公仔,將為文創產業注入一股新活力。 |
|
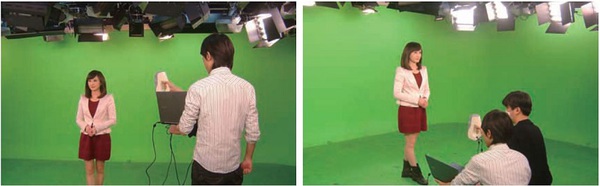
圖五 : 3D公仔列印前的掃瞄工作,360度都必須完整掃瞄。 |
|
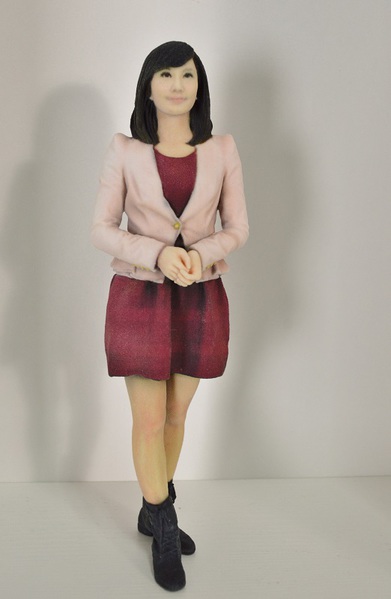
圖六 : 經過細部處理與上色,縮小版的人形公仔就此完工囉。 |
|
結語
用3D列印進行直接製造,的確有助於打開3D列印的一扇商機大門。3D列印從大量生產的角來看,或許真的就如郭台銘所說的,只是噱頭而已。但若換個角度來看,3D列印的確也有其能大大發揮的空間,特別是在小量生產與原型設計,以及單一客製化等市場。不久的未來,當3D列印走向直接數位製造之後,普羅大眾將更有機會『直接』從3D列印上獲得利益。