利用卷筒狀塑膠基板與印刷技術,直接將矽半導體或是金屬材料,如同印刷報張雜誌般,製作類似厚度只有0.6mm的液晶顯示器、1/10重量的太陽光電板,以及如同衣服般柔軟的感測器等電子產品,如(圖一),進而取代傳統真空、濺鍍、光阻、蝕刻等製程,亦即所謂的「次世代科技-電子元件印刷技術」,最近幾年成為全球囑目的焦點。利用上述全新的製作觀念製成的電子產品,具有輕薄、可撓曲,以及低單位面積製作成本、可大型化等特點,未來甚至可應用於非揮發性記憶體,與高頻無線tag等領域,如(圖二),因此國外各大公司相繼加入研發行列,有鑑於此本文將介紹電子元件印刷技術的最新發展動向。
印刷技術發展經緯
如(圖三)所示利用印刷方式製作電子元件,主要理由是它可以大幅改變傳統技術的製作方法與使用的材料,尤其是材料的改變更可獲得單位面積的製作成本,與輕巧薄型化雙重效益,如(圖四)。
製程上的變革有兩項,分別是電路pattern的製造方式的改變與基板結構的改變。第一項是利用半導體或是金屬材料,在基板上直接描繪電路亦即「直接描繪技術」;另一項是基板結構改變,它是改採長達數百公尺卷筒狀基板,利用所謂的role to role方式,以連續複數製程完成元件的製作。
傳統電子元件的製作為了形成電路pattern,必需使用非常複雜的製程技術,通常會先在基板上製作由半導體或是金屬構成的電路膜層,接著在膜層上描繪電路應用範圍,最後再刻繪成電路,整個過程如同先將紙張表面塗黑,再逐一去除文字以外的黑色部位。
為了達成上述目的,電子元件的場合必需使用高單價,且體積龐大的真空設備,相較之下直接描繪方法有如直接描繪文字,它可以利用轉寫手段描繪出電路pattern,使得傳統濺鍍、光罩、蝕刻三個工程被簡化成一個,而且製作過程可在大氣環境下完成,不需使用任何高單價真空設備。除此之外傳統製程的基板處理所需的over head非常大,主要原因是製程上使用切割狀的基板,因此必需設置各工程之間的基板搬移,以及基板的進出空間。
role to role方式的基板則是在各設備之間連續移動,加上製作設備被連成一體,所以空間以及基板搬送等問題都可獲得徹底解決,如果合併使用role to role與直接描繪兩技術時,更可以大幅簡化繁瑣的程序與設備投資並提高量產性。
有關印刷技術的單位面積製作成本,雖然會隨著元件的種類與量產規模而異,根據初步試算結果顯示,例如以印刷電路為例,合併使用role to role與直接描繪技術,可使製作成本降至1/3以下,若是製作液晶顯示器與LSI的場合,製作成本可望壓縮至千分之一甚至萬分之一以下。
值得一提的是利用次世代印刷技術是製作電子元件時,基於輕薄可撓曲等訴求,傳統的半導體、導線與基板使用的材料必需改變,例如玻璃、半導體基板會變成塑膠基板,半導體與導線則變成有機半導體與金屬微粒子。尤其塑膠基板的厚度比矽半導體基板與玻璃基板少一位數,比重只有一半左右,因此製成的電子元件非常輕巧。
東京大學利用塑膠基板與有機半導體試作的壓力感測器,即使捲繞於鉛筆上亦無破損之虞、此外飛利浦即將量產的電子紙,安全撓曲曲率半徑更高達2cm。
未來發展動向
如上所述印刷技術製作電子元件具有許多優點,不過反面是距離實用化仍有幾項障礙(hurdle)有待克服,因此部份廠商計劃先建立關鍵技術,日後再與周邊技術整合,事實上即使是部份印刷技術,已經對廠商產生實質助益。富士電機將太陽光電板與TRADIM(次世代可攜式顯示用材料技術研究小組),將液晶顯示器用的role to role技術列為最優先研發項目,有機半導體的直接描繪技術更被列為前瞻研究範疇;Albac、Epson、大日本印刷等公司,則是全力投入直接描繪技術實用化的研究。
不論是「role to role」方式或是「直接描繪方式」,兩者面臨最大問題是如何建立高頻電晶體的製作技術。計劃採用role to role方式的廠商,試圖利用真空製膜技術解決上述問題;採用直接描繪方式的廠商,則以各別塑膠基板提高性能的手法因應,不過以上兩者卻不約而同計劃以製作上比較容易的簡易matrix type EL有機顯示器、太陽光電板、電子紙作起始,再逐步朝結構複雜的高速電子元件,以及液晶顯示器方向發展。
雖然role to role方式未來可應用於電晶體的製作,不過目前TFT電路仍以矽半導體電晶體為主,一般認為未來液晶顯示器相關元件,可望全部利用role to role方式貼合製成,只有彩色濾光膜片(color filter)基於製程上受限於真空設備,因此只能使用直接描繪技術製作。
液晶顯示器的TFT電路若在大氣環境下,利用直接描繪技術製作,必需使用載子(carrier)移動度極高的有機半導體,不過目前尚未發現可以滿足所有性能要求的材料,因此Tradin改用其它方式,具體方法是在塑膠基板上製作矽膜層,然而實際上卷筒狀塑膠基板並無法承受長膜時的高溫,因此具備250度耐高溫塑膠基板問世之前,Tradin計劃開發新技術,將玻璃基板上形成的TFT電路膜層,依照(圖五)所示黏貼於塑膠基板,包含反射膜與配向膜在TFT電路膜層的總候度約為0.2mm左右。不過上述黏貼替代方案只是過渡期技術,最終目標是TFT液晶顯示器全部利用印刷技術製作。
利用印刷技術製作電子元件主要得力於材料與加工技術的進步,其中又以加工技術最顯著,因此製作各種顯示器、太陽光電板、無線tag所需的高精度直接描繪技術幾乎非常完備。製作如此電子元件所需的最小加工尺寸,以電晶體為例5μm配線部份的最小加工尺寸大約是20μm。目前有機半導體與金屬微粒子直接描繪方法可分成四種,不過實際上滿足(表一)條件的技術卻遠超過上述四種。
在塑膠基板上製作有機電晶體時,材料塗佈於基板表面不可施加壓力,因為反覆塗佈複數的電極與半導體材料,若殘留應力會造成電晶體的品質劣化,這意味著符合此條件的製作方法將受到限制;此外噴墨技術(ink jet)與網版印刷以及凹版(gravure)印刷技術,相異層間的位置偏異也一直受到質疑與爭議。
噴墨方式可根據CAD資料直接描繪pattern,由於無網版問題因此非常適合少量多樣生產;網版印刷以及凹版印刷技術有製作原版的困擾,不過反面是所有電路pattern可利用原版一次完成,因此具有極高的量產效益。除此之外也可以利用模版壓製方式,製作10μm以下的pattern線寬,亦即所謂的「Imprint技術」最近備受相關業者高度囑目,不過Imprint技術程上基板會殘留應力,所以不適合電晶體(transistor)的製作,比較適合應用於印刷電路板嶼電子元件的佈線等領域。Imprint技術可獲得與原版幾乎一致的pattern,一般認為佈線寬度可望低於10μm,事實上最小加工尺寸70nm的製作設備,已經進入商品化階段(圖六)。
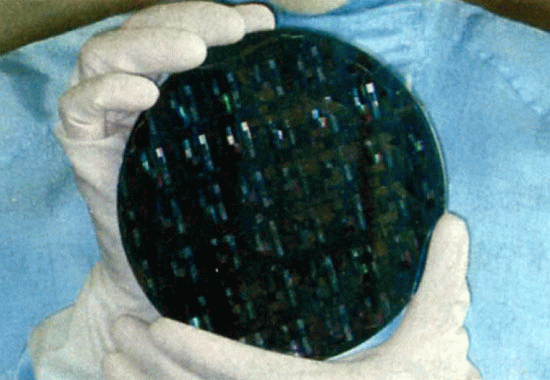
《圖六 利用Imprint技術製作的寬70nm pattern外觀》 |
|
利用印刷技術在基板製作電子元件是否能實用化,取決於有機半導體與微粒子材料技術的進展,尤其是動作頻率高達MHz電晶體的有機半導體材料的開發,更是具有決定性的影響。
雖然部份廠商嘗試利用有機半導體材料在塑膠基本上製作二極體、電阻與電容等各別獨立電子元件,不過有機電晶體的動作頻率非常低,因此利用以上方式製成的電子元件即使組成電路(圖七),往往無法獲得預期效果,嚴重時甚至不會動作。
目前利用有機半導體與直接描繪技術製成的電晶體,動作頻率大約是100kHz,雖然電晶體的動作頻率隨著用途有極大差異,不過基本上未來必需提高一位數以上。
2003年12月美國3M曾公開表示有機電晶體可作1MHz的動作,這意味著未來非結晶矽(amorphous silicon)主動式液晶顯示器、有機EL顯示器,以及電子紙甚至矽基板製成的125kHz、530kHz無線tag,都將成為有機電晶體的應用範圍,如(圖八)。
不過,目前使用的有機電晶體是利用真空設備製成,因此無法應用直接描繪技術加工,所幸的是最近五年有機半導體的載子移動度提高二位數左右,2005年已可利用直接描繪技術製作動作頻率為1MHz的有機電晶體。
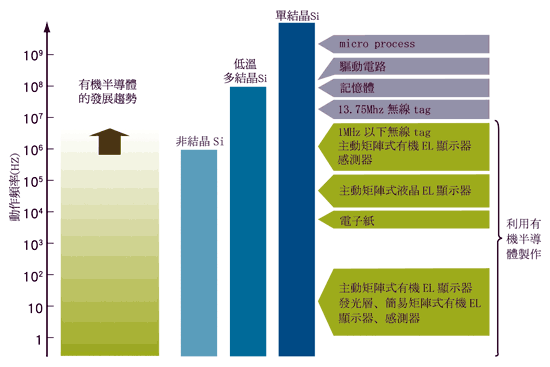
《圖八 有機半導體可望取代所有傳統矽半導體電子元件》 |
|
有關佈線用金屬微粒子的發展,已經在各種用途上達到實用化水準,因此直接描繪加工技術可選擇的範圍更加寬裕,以往直接描繪大多使用Ag金屬微粒子,2004年出現的Cu金屬微粒子加入,使得流通電流的印刷電路板受益最大。
因為Ag金屬微粒子即極造成電子遷移(electro migration)與斷線,因此不適合大電流用途,如果改用Cu金屬微粒子除了可以解決上述問題之外,更可當作各種電子元件的配線,徹底杜絕斷線困擾。
利用Cu金屬微粒子製作印刷電路板的佈線時,由於電路基板必需加熱至250℃~300℃,因此無法合併使用「直接描繪加工技術」與「role to role加工技術」,因為如此高溫塑膠基板會遭到破壞無法使用,如果Ag與Cu金屬微粒子的加工溫度不超過200℃,基本上可以融著於塑膠基板表面,因此未來必需開發低溫Cu金屬微粒子。
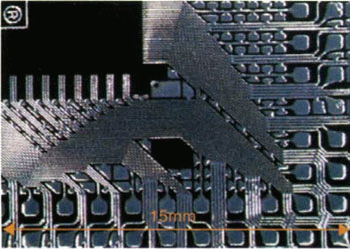
《圖九 利用金屬微粒子製作印刷電路板的佈線pattern》 |
|
結語
隨著科技的進步小型、輕巧、可撓曲已經成為電子產品的專有名詞,這意味著傳統的電子元件加工技術與觀念即將面臨革命,今後類似印刷技術製作電子元件新技術會陸續問世。