为可容纳来自合作夥伴前所未有的多种反应室的类型、尺寸和配置,应用材料公司最新推出10多年来最重要的晶圆制造平台创新方案Vistara,便强调专为晶片制造商提供必备的灵活性、智慧功能及永续性,以解决日益严峻的晶片制造挑战。
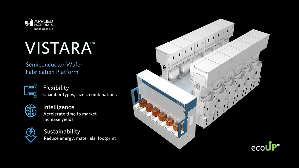 |
应材公司Vistara,专为提供灵活性、智慧功能及永续性而设计的平台 |
应用材料公司表示,Vistara平台的开发基础系建立在该公司长期以来在半导体制造平台领域所保持的领先地位,包含Endura、Producer、Centura和Centris等平台,已广获全球各地的晶圆厂使用,且几??生产了所有的晶片。
最新Vistara平台的开发时间则长达4年以上,叁与人员来自应用材料公司的硬体、软体、制程技术和生态效率(ecoefficiency)设计团队的数百名工程师,可支援使用应材及合作夥伴所提供前所未有的多种反应室类型、尺寸和配置,配置4~6个晶圆批次装载埠,并以最少4个、最多12个制程反应室来处理各种不同的工作负载。既能接受用於原子层沉积和化学气相沉积等制程的小型反应室,也可以容纳用於磊晶和蚀刻等制程的大型反应室。
应用材料公司半导体产品事业群总裁帕布·若杰(Prabu Raja)博士表示:「Vistara平台与其前代方案相同,旨在成为客户创新、可靠和生产力的长年信赖平台。当半导体产业在复杂性、成本、节奏和碳排放方面,面临日益增加的晶片制造挑战之际,具备高度灵活性的Vistara平台问世恰逢其时。」
该公司与客户得以藉此结合这些反应室,为晶片制造商开发前所未见的整合型材料解决方案IMS(Integrated Materials Solution)配方,从而在真空环境下,於同一系统中完成多个连续的晶圆生产制程步骤,能协助晶片制造商开发创新的电晶体、记忆体和布线,提升效能和功率,并防止影响良率的微粒和缺陷。
此外,Vistara平台同时配置了数千个感测器,能将大量数据即时传送到应材的AIx和EcoTwin软体平台,专门用来协助降低半导体制造对环境的影响;同时涵盖了研发、制程转移和扩产、大量制造等应用领域,藉其智慧功能可加速上市时间、最大化大量制造的产能和产量,帮助客户解决持续增长的晶圆制造节奏和成本挑战。
经过从数千个制程变数所取得的可操作数据,发挥工程师能运用机器学习和人工智慧的强大功能,加速开发制程配方,实现最隹的晶片效能、功率和最大的制程容许范围(process window)。如今,首批Vistara平台已交付给所有记忆体客户领导大厂,用於蚀刻应用。应材预期随着晶圆制造设备业为满足全球半导体需求而成长时,其所有主要平台的解决方案也将同步成长。
将此智慧功能导入整个平台之後,可在工厂介面模组中智慧控制负载锁定(load locks),以优化抽气和排气时间,帮助晶片制造商减少微粒和缺陷,达到最大化良率;以及平台机器人自动校准,降低启动时间75%。Vistara平台在生产过程中,还会持续监测和校准其组件,以最小化人工干预、最大化正常运作时间,并预测维修需求。
然而,基於半导体制程的复杂性和步骤,增加了生产每片晶圆所需的能源和材料,Vistara也是首座专为推进应材「3x30」倡议而设计的平台,协助客户实现永续目标而设计。与之前设计相比,旨在2030年之前将同等能源、化学品消耗量减少50%以上;以及系统的无尘室占地面积要求减少30%的建筑材料消耗量,将有助於每月生产10万片投产晶圆(WSPM)的晶圆厂节省100万公吨的碳排放。
工程师为此彻底重新设计Vistara平台的气体控制板,同时优化了该平台对能源密集型附属制造区(Sub-Fab)组件的使用方式,包括泵浦、热交换器和冷却系统,比起先前平台的能源消耗降低至35%;同时帮助晶片制造商,减少其在范畴1和范畴2的碳排放,以协助客户在较小厂房中生产更多晶圆,并减少使用如混凝土和钢材等碳密集型建筑材料,。
应材还进一步推出了生态效率软体EcoTwin,并首先在Vistara平台上提供。让制程工程师能藉由EcoTwin分析表上,比较替代化学物质、配方和生产技术的碳排放影响性,以持续改善整个制程节点生命周期内的永续性,并追踪和呈报实现永续目标的进度。并利用EcoTwin软体利用感测器数据,协助工程师监控反应室、系统和厂务区区组件的即时能源和化学品消耗情况。