科盛科技宣布推出新一代的模流分析软体Moldex3D R17,协助全球各产业客户透过数位化转型,加速推动智慧制造 。以虚实整合为主轴,最新版Moldex3D以更全面、更真实的模拟技术,拉近模拟端与制造端的距离。全新的使用者介面及一站式的模拟流程,提供更强而有力的模拟洞察,加速产品决策过程。同时,因应汽车与航太产业无止境的轻量化需求,在复合材料的模拟能力上也有多项突破性的发展,满足复材产业多元化的制造需求。
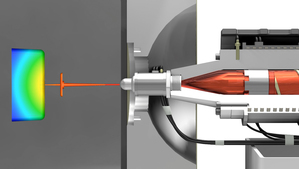 |
/news/2019/04/08/1332094750S.jpg |
科盛科技总经理杨文礼博士表示:『新版R17是Moldex3D的一个重要的里程碑。无论是设计端、制造端还是模拟端,都将受益於Moldex3D更全面的虚实整合能力和更即时的产品洞察反??,进而提升智慧制造能力,强化市场竞争力。』
Moldex3D R17版本的重要更新及亮点如下:
为了进一步破除模拟和实际制造之间的隔阂,新版Moldex3D大幅度提升虚实整合能力,扩大模拟软体整合真实世界资讯的能力。Moldex3D R17能协助用户监定和考虑现场射出机台的动态响应特性,进而提供符合实际生产所需的成型条件优化结果。现场人员可以直接应用Moldex3D提供的优化结果,使模拟结果和实际制造更一致。除了机台特性,模拟材料的真实行为也是Moldex3D改版的重点之一。Moldex3D料管压缩功能可以模拟材料在射出成型机台的料管及喷嘴阶段经历的压缩行为,以利更真实考量材料在进入模穴时所受的材料压缩性影响,协助用户更精准评估射出压力。透过更紧密的虚实整合,让Moldex3D用户可以直接应用模拟数据,做出更好的制造决策。
此外,Moldex3D提供详尽的水路分析数据,包含:最大压力、整体流量及散热量,以利用户评估合适的模温机规格,更精准掌握模温机的实际表现,避免和预期的冷却效果造成落差。
材料和制程是实现轻量化的至要关键,而在转换轻量化材料和制程的过程,模拟软体则扮演不可或缺的要角。新版Moldex3D首创领先业界的流动-纤维全耦合分析,能精确捕捉及预测由纤维配向引起的非等向性流动行为,针对纤维浓度高和纤维配向预测精准度需求高的复合材料产品,无疑是一大利器。除了新的耦合技术,R17 纤维配向分析新增支援扁平玻璃纤维,助力产品设计人员在实际生产前透过模拟分析评估材料选择,提升尺寸稳定性并且降低翘曲变形。
在先进轻量化制程部分,Moldex3D材料实验室提供深入的化学发泡材料量测,可以获得重要的发泡材料叁数,包含发泡倍率。Moldex3D R17化学发泡分析将发泡倍率叁数也纳入模拟考量,使发泡高度和形状的预测结果与现实更相符。此外,在树脂转注成型(Resin Transfer Molding)的使用介面也有显着改善,简化网格生成流程,提升模拟效率。
如何提高软体的易用性,协助客户更快速、更轻易地将模拟数据转换为有用的产品洞察,一直是Moldex3D研发团队的重要使命。新版Moldex3D R17在Studio平台上实现了一站式模拟流程,大幅强化了使用者和模型之间的互动。针对棘手的产品收缩问题,Moldex3D Studio 提供量测距离(Measurement)和缩放(Scale)功能,让用户能够直接量测产品收缩范围,并立即进行产品设计变更,完成翘曲补偿收缩。
另外,透过新的可视化工具和後处理图表,以及更快的图形显示效能,使用者可以更快速、更深入挖掘隐藏在模型背後的设计洞察,有效降低生产风险,加速产品开发周期。