|
工業4.0環境下的自動化系統重新定義 |
【作者: Suhel Dhanani】 2017年05月03日 星期三
|
|
瀏覽人次:【16252】
麥肯錫公司(McKinsey)在最近的一份報告當中,將工業4.0定義為「製造業的數位化,幾乎所有產品部件和製造設備中都有嵌入感測器,無所不在的資訊物理系統,以及所有相關資料的分析。」雖然McKinsey的這份報告對工業4.0的分析大部分都重點集中在提高資料獲取/分析以及由此為固定資產以及業務優化帶來的好處,但其中也強調了嵌入式智慧感測器對工業4.0的支持作用。該報告在此基礎之上,重新定義了支持工業4.0的自動化系統的架構。
在各種關於工業4.0的討論中,有時會遺漏一項關鍵觀點:數位工廠不僅僅製造產品,而且實際上也是一個資訊收集和處理實體。這種觀點說明,為了梳理出各層之間的關係以及進行優化,(幾乎)要對所有一切進行檢測、測量和處理。支持這種數位化、智慧化工廠的系統無論在數量上還是複雜性方面都有所不同。例如,工廠車間的感測器數量發生爆炸式成長,而且處理和通訊能力也發生巨大變化;控制系統更多地呈現分散式而非中央式—改變了其通訊、規格及耐用性要求;設計之初就考慮了通訊功能(例如不存在氣隙)的系統在DNA中已經具備了嵌入式安全架構。
本文介紹支援工業4.0的新興系統設計趨勢。
工業4.0就在我們身邊
數位化工廠的例子有很多,都體現了工業4.0的概念,展示了這種超自動化帶來的利益。
西門子(Siemens)公司在德國安貝格的一家工廠2採用的生產方法可視為是工業4.0的精髓。該工廠生產包括Simatic可程式設計邏輯控制器(PLC)在內的各種系統。生產過程的自動化程度很高,機器和電腦負責處理75%的價值鏈。大約1000台Simatic控制器本身管理Simatic設備的生產。
如此高度自動化大大提高了生產力,讓工廠的產出提高了8倍。工廠每年生產接近1500萬台Simatic產品—相當於每秒輸出一台控制單元。這使得生產品質達到了前所未有的99.99885%。
這僅僅是工業4.0在實際應用中的一個例子。本例中雖然沒有明說,但不難看出自動化系統本身架構的變化。從該工廠的描述中,可梳理出系統架構的三大特性:
‧ 使用了1,000台分散式控制器—不是一台中央式、巨型、機櫃大小的PLC
‧ 機器負責處理75%的製造過程,必須通過大量感測器獲得資訊。
‧ 這些感測器必須傳遞豐富的資料—不僅僅是「發熱」或「不發熱」,而是(譬如)電機的準確溫度。
工業4.0在GE的噴氣式發動機上也顯示出了其魅力,該發動機設計不但具有最大的推力,而且具有最大的資料收集能力。GEnx噴氣式發動機包含26個感測器,測量300個參數,取樣速率達到16採樣/秒—使GE能夠在一次普通飛行中處理150M單位的資料3。與前一代噴氣式發動機相比,該發送機的燃油效率提高15%,並且有望通過預測性維護縮短停工時間,使其成為GE Aviation歷史上銷售最快的發動機。
本例又一次說明了利用智慧感測器發送生產過程中(本例中為複雜的噴氣式發動機)的智慧、詳細的性能參數的重要性。McKinsey公司近期的另一份報告中介紹了更多的工業4.0例子4。
工業4.0推動工業感測器設計發展趨勢
工業4.0之路預示著工業感測器設計領域的兩大趨勢:感測器變得越來越小巧、收集/發送的資訊越來越豐富。直接影響這兩項系統級趨勢的因素是收集和分析工廠中不斷成長的資料量的需求—這是工業4.0的關鍵。
其中一個很好的例子是小尺寸、高度整合智慧感測器的應用,這些感測器通過一定的協定發送豐富的資訊,比如IO-Link—工廠自動化系統領域成長最快的感測器通訊協定。
為了收集和發送更詳細的資訊,就需要開發簡單、可靠且高效的通訊協議,例如IO-Link,以滿足工廠車間的應用。
從上世紀80年代以來,工業現場匯流排已經支援智慧設備、較快地安裝、減少接線,並且更容易維護。然而,統一、普遍可接收的現場匯流排的缺失,也引起了混淆、培訓挑戰、高成本以及設備之間相容的問題。IO-Link是第一種開放式、現場匯流排不可知、低成本、點對點串列通訊匯流排協定,用於與感測器及執行器通訊。
這種功能強大的點對點通訊協議基於成熟的3線感測器與執行器連接,已經被採納為國際標準(IEC 61131-9),用於感測器與執行器通訊。理解IO-Link通訊的最好方式是將其理解成感測器領域的USB—非常容易使用和部署,並且能夠提供來自於智慧感測器的智慧資料。
我們看到,自動化系統廠商開發和推廣基於IO-Link的智慧感測器整體方案,以推動其「互聯企業」的願景—Rockwell Automation用來表示新一代數位工廠的術語5。我們接下來看幾個這種新興感測器系統的例子。
圖1所示為微小的IO-Link接近檢測感測器,備有紅外收發器、配套IR LED驅動器、IO-Link收發器以及高能效的降壓轉換器,全部安裝在8.2mm x 31.5mm印刷電路(PC)板上。高度整合的半導體允許我們在如此小的尺寸內構建整個感測器子系統。
接近檢測感測器檢測是否有某個物體接近,所以能夠透過發送表示接近的簡單數位訊號(開/關)來打開去路。然而,在很多情況下,現代化感測器必須檢測和發送更豐富的資訊—例如檢測到的顏色、實測溫度或到某個物體的距離。圖2所示為高精度IO-Link電阻溫度檢測器(RTD)溫度感測器參考設計,用於配合2線、3線或4線PT100 RTD使用。該系統利用整合式RTD至數位轉換器以及最新的IO-Link方案來提供高精度溫度值,解析度高達15位。
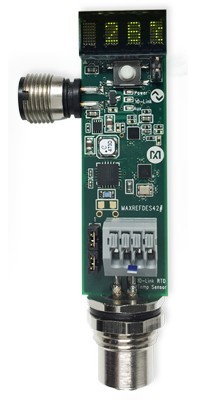
圖2 : Maxim的高精度IO-Link電阻溫度檢測器(RTD)溫度感測器參考設計 |
|
|
分散式控制的優勢
工業4.0引發的系統架構的另一種變化是分散式控制器使用越來越廣。由於工廠/過程中的感測器數量眾多,不可能將每個感測器都連接至中央PLC,而是將許多分散式PLC靠近受控制的線路。工業4.0配置中的PLC必須是小型的,以便將工廠中現有中央式機器控制的工業計算能力轉移到更靠近工廠車間的實際機器。
這樣能使工廠具備更高的製造靈活性,對每條組裝線的健康和狀態具有更高的可視性。通過部署大量分散式微型PLC,允許客戶快速作決策,從而優化產量、配置感測器/執行器,以適應不同的產品選項,並收集智慧資料供雲端分析。擁有1,000台分散式PLC的Siemens安貝格工廠就是很好的一個例子。這意味著我們需要功能強大但尺寸又非常小、能源效率高的PLC系統架構。
為了縮小PLC的尺寸,最大的問題在於減小類比及混合信號電路的規格。大多數工程師仍然認為數位技術提供了節省空間的最佳機會,然而數位晶片一般僅佔據很小一部分,大約為PLC模組中15%至20%的電路板空間(圖3)。圖中所示為Maxim Integrated的微型PLC (Maxim的一種技術演示平台) IO模組內的類比和數位功能估算情況。
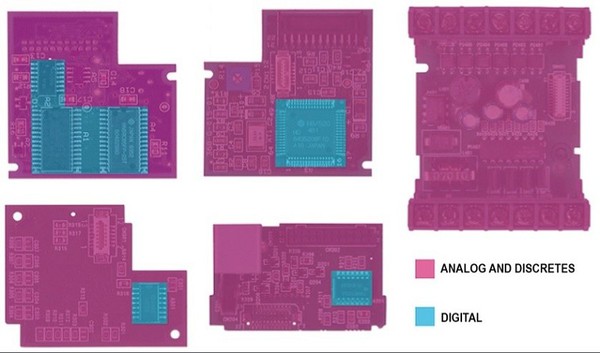
圖3 : 微型PLC中的系統整合挑戰顯而易見,系統電路板上的類比和數位元件都清晰可見。 |
|
類比器件佔據了高達85%的PLC模組可用電路板空間,但並不像數位晶片那樣具有規模。智慧類比整合,例如整合IO器件或LDO與RS485器件的隔離,是構建功能強大且小尺寸分散式控制器的關鍵,這是工業4.0的重要特徵。
Maxim已經走在了智慧類比整合的前列,通過技術來展示其先進的類比晶片如何?明構建世界上最小的PLC。在2014年的電子展覽會上,Maxim展示了掌上型微型PLC演示平台,該平台擁有24路IO通道,其中包括數位、類比及IO-Link IO (見圖4)。
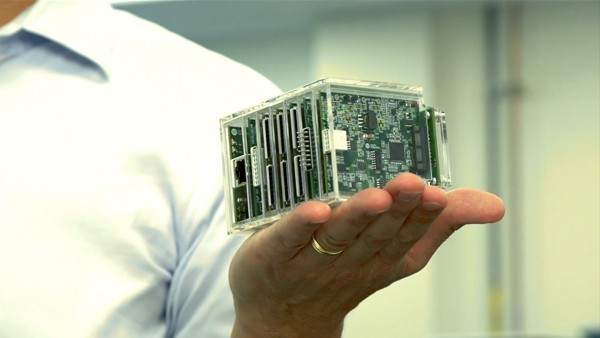
圖4 : 利用整合類比技術,大幅縮小微型PLC—Maxim技術演示平台。 |
|
2015年,Maxim引入了一種名為Pocket IO的新型PLC開發平台,又跨上了一個新臺階。
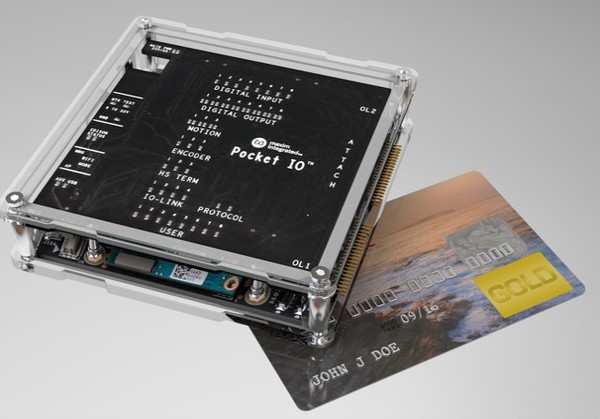
圖5 : Maxim的最新PLC開發平台—Pocket IO |
|
什麼是Pocket IO?
Pocket IO是下一代工廠中分散式控制器配置形式的例子之一。與Maxim的上一代微型PLC平台相比,該控制器平台尺寸減小了2.5倍。平台擁有超小尺寸的外形尺寸:不到10立方英寸(9.8立方英寸)。
Pocket IO不但總系統的尺寸小,而且得益於Maxim專有的類比製程技術,其工業電源產品效率高於90%,所以平台的電源尺寸減小了30%。Pocket IO的靈活配置擁有超過30路IO,可配置為支援工廠/過程自動化組裝線,以及控制其它系統,例如機器人和樓宇自動化。Pocket IO的規格和電源特性得益於超過50種Maxim IC的協同工作。
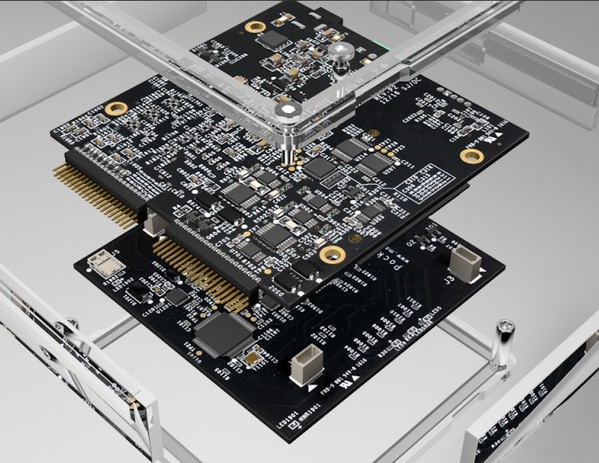
圖6 : 超過50片Maxim IC協同工作,成就了Pocket IO的架構 |
|
利用Arduino整合式開發環境,很容易對Pocket IO進行程式設計;該開發環境是用於Pocket IO的免費應用程式,應用廣泛,很容易上手,並且開發快速。選擇該程式作為軟體環境的原因是其被全球廣泛採用,並且作業系統相容性好,支援Windows、Mac、及Linux作業系統。
利用下一代自動化系統實現工業4.0
Maxim的產品滿足下一代自動化系統要求的小尺寸、低功耗。這些系統必須尺寸小巧、無源冷卻(所以功耗較低),並且足夠智慧,能夠制定本地控制決策,收集智慧過程資訊並向上傳輸。Maxim已經擁有了大量的此類系統—無論是Maxim自行開發的參考設計,或是由知名的自動化廠商開發,例如SICK和Rockwell Automation,以搭建全自動化的足球測試工廠。
通過大量支持IO-Link的感測器和高性能Pocket IO平台,該工廠測試規定大小足球的重量、彈跳高度、外形以及壓力。整個流程都通過iPad控制,以無線方式連接到已聯網的工廠。
這種高度自動化數位工廠是工業4.0的集中實踐—自動化組裝線通過支持IO-Link的感測器為本地、分散式控制器(Maxim Pocket IO演示平台)提供豐富的資料。所有決策都在本地快速完成,工廠回應生產要求的方式非常靈活。在各種子系統中,使用了超過100種Maxim IC來控制、檢測以及更新支撐工廠運轉的自動化系統。
(本文作者Suhel Dhanani 為Maxim Integrated控制和自動化戰略部技術團隊主要成員)
參考網址
1 https://www.mckinsey.de/sites/mck_files/files/mck_industry_40_report.pdf
2 http://www.siemens.com/press/pool/de/events/2015/corporate/2015-02-amberg/factsheet-amberg-en.pdf
3 https://www.youtube.com/watch?v=2Jqhld45iko
4http://www.mckinsey.com/business-functions/operations/our-insights/manufacturings-next-act
5 http://literature.rockwellautomation.com/idc/groups/literature/documents/br/iolink-br001_-en-p.pdf
|