德國在2012年提出工業4.0概念後,各大製造設備供應商與各國政府紛紛跟進,提出類似的智慧製造概念政策,雖然各國政策內容不一,不過仍有其交集之處,現在的智慧製造概念,是讓製造業中各企業運作包括IT與OT各環節的數據可被擷取、儲存、運算、分析,再依需求做出各類決策與指令,而要達到此目標的前提是,所有數據都必須數位化,透過數位化,後端的系統才能進一步處理相關資料,也因此,數位化會是打造智慧工廠的第一步。
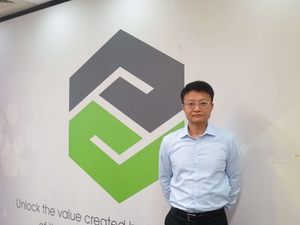 |
/news/2018/03/27/0844029560S.jpg |
數位化技術在產品設計端的應用已早,近年來無論在技術或應用都仍持續強化,PTC I*Center Taiwan MCAD技術總監鄭景懋指出,過去的設計多只能靠經驗傳承,透過數位化,則可以將這些無形的經驗完整保留,且具體的再次呈現,同時透過數位工具的邏輯判斷,讓設計者在設計時,對產品更有洞察力、更理解產品。
他以PTC的CAD平台Creo 4.0在賽車設計為案例指出,Creo 4.0在2017年加入可結合AR與IoT應用的Digital Twin解決方案,可為客戶帶來更精準的設計,過去的賽車設計,都是設計師在電腦上模擬車體與環境的狀況,像是引擎中的進氣閥角度、氣流、溫度等,最後再將結果輸出,製造出實體車輛,並讓車輛在路上反覆實測,逐步調整各部件的位置,此一過程必須不斷重複,且未必能調整出最精準的設計。
Digital Twin的方式則是在車體各部件中建置感測器,由感測器紀錄引擎進氣閥的各種連續數據,在電腦系統中建立起數位模型,設計師可依據來自現實運作的數據,讓設計可以一步到位的貼近實際應用狀況,不再經過重複的假設與調整流程,不但可縮短產品上市時間,同時還提升產品品質。