由於在工廠生產過程中,加工設備故障往往會產生長時間生產停止的狀況,因而嚴重影響生產效率與設備稼動率,CTIMES與智動化雜誌於今舉辦科技論壇,針對次世代工具機設備的關鍵技術趨勢進行深度剖析。
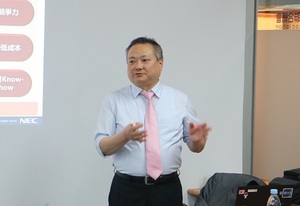 |
相馬知指出,透過及早預測故障或異常,將可防止意外停機,以提高運作率、優化生產。 |
此次論壇不僅邀請到工研院巨量資訊科技中心藍坤銘副組長、中正大學
機械系特聘教授鄭志均博士、寶元數控副總經理施正修,更特別邀請日本電氣株式會社 AI Analytics事業開發本部資深資料分析師相馬知也,剖析從感測器、AI、IoT等技術,如何實現設備監視及產品生命週期預測。
工研院巨量資訊科技中心技術副組長藍坤銘博士指出,由於現今製程越趨複雜,傳統統計分析逐漸無法解決產業面臨的各項問題,因此,他直指,巨量分析與AI技術將成為解決產業問題的關鍵。
寶元數控副總經理施正修也指出,相較於以往的精密機械,加入控制器核心、感測器、物聯網及大數據等智慧技術,經由分析各項數據所呈現的狀況與原因,協助人員進行機械停機原因偵測,並透過資料分析達到預防與自適應解決。
此外,施正修更針對常使用於工具機的三大感測器-壓力感測器、溫度感測器及震動感測器進行進一步說明。
施正修指出,相對於傳統機台只能倚靠加工成品進行確認,或仰賴人員巡邏觀察機台狀況,加裝感測器的智慧機械,可自動在加工過程中在線檢測機台狀況,將大量降低問題發生的反應時間,提升機台稼動率。
另一方面,相馬知也更特別針對如何透過不變量,實現設備高度監視與品質劣化及早檢知進行解說。
他說明,以往由人員進行運作監視,難以全面且持續監視未達警報值的異常預兆,若透過不變量分析的協助,將能及早發現與平常不同的行動,及時、全面且持續地掌握變化;此外,透過「要素分析技術」將可找出導致變化的要素,將以往無法特定的變化要素和影響程度明確化。
透過上述各項技術,經由各式感測器與功能平台的協助,並結合物聯網與人工智慧技術,取得工廠機器中的各項數據並加以分析,再比對生產設備所使用的零件生命週期資料,將有可能精準分析設備劣化程度,並進行生命週期預測。