面對後疫時代及全球供應鏈重組趨勢,導致製造業在營運上越發受到外在環境快速變化的考驗,產品庫存或產能過剩的問題接踵而來,也順勢催化產業須加強數位轉型的進程,首先要讓工廠數據可視化,接著才是導入AIoT智慧化,並搭配PLC兼顧彈性與高穩定度。
基於現今製造業應用領域廣泛,對於加工產品的品質、產量、價值越來越高,更加深人力與物料的雙重挑戰,終端加工廠商邁向工業4.0階段為了能預診系統故障,在加工尚未發生不良品或導致整機損壞前,即能優先排除問題。因此透過在機台上安裝多樣感測器,並搭配各種邊緣(Edge)人工智慧(AI)演算法、模型,以有效監測作動效能;進而上傳雲端(Cloud)示警或快速規劃保修程序、避免意外停機,從而提升機械設備總體效率(OEE)的高精密與高穩定性,實踐節能低碳目標。
惟當OEM機械設備製造商在投入研發、提升設備性能的同時,也必須透過數位化強化內部營運,創造競爭優勢。透過MEMS感測器直接蒐集、分析資料的好處固然方便,也不必大幅更改機構,並避開PLC控制器的系統封閉性或保護裝置,整體成本低於通過PC-based架構控制器讀取運作資料。
但缺點卻存在資安風險較高、不穩定;以及企業開始面臨大量資料的撈取、篩選、標記、分析過於複雜等課題。且因為系統運作中有太多非結構式資料,恐無法透過原始資料瞭解系統性能,或是成本過高;以及某些設備發生問題前近乎沒有徵狀,必須透過一些特殊演算法、長期監測以取得系統平常運作曲線,建立正常值/非正常值的邊界。
大部份傳產製造業者也無力建置大量運算能力的機房,現今PLC相較於搭配PC-Based控制器的運動控制軸卡、閘道器等,性能早已相差無幾且更為穩定、可靠。此時即可透過AI模組將感測器的資訊篩選後再上傳雲端,或利用Edge AI判斷系統的失效模式,執行預防性維護。
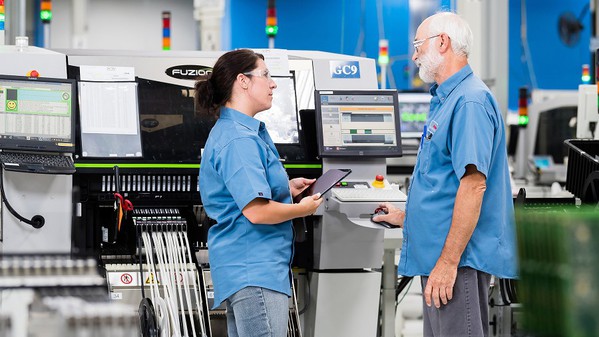
圖1 : 現今PLC相較於PC-Based控制器,性能早已相差無幾,且更為穩定、可靠。(source:rockwellautomation.com) |
|
台達首要透過可視化 打造新一代智能工廠
目前台達旗下工業自動化的產品布局,即可由下而上概分為最底層的系統設備、感測儀表/控制器PLC、網路通訊、製造管理、資料分析/系統優化等,皆由自主研發製造;再經過各廠區、產線率先導入自家設備自動化、製造生產管理平台,藉以即時蒐集生產資訊,實現更完善的人機料法環管理。
其秉持簡單化/合理化智慧製造為基礎,選用標準化、模組化零組件,提高台達軟韌硬體的管理效率,確保所有功能可被重覆利用,避免過度開發。最後在製程中納入「數位分身(Digital twin)」的數位化、虛擬化概念,利用設備連網蒐集到數位化製程資訊,再經虛擬整合建模來模擬最佳化參數,減少錯誤設計,以及對於硬體環境依賴和建構成本;同時透過系統間自動交換Raw Data資料奠定分析基礎、加速邁向智能化,以利後續實現自動化及製程優化目的。
台達進一步指出,現今工業物聯網應由需求價值驅動,要從自動化轉型資訊化過程中的關鍵是IT+OT有效融合硬體、系統、文化3元素的數位轉型趨勢不可擋,已有越來越多實體組成物物相連的網路系統,並透過數位化在虛擬化網路空間進行管理和監控。
其中的「系統」則依序包括底層的IIoT平台/邊緣運算;中層製造執行系統、品質管理系統、設備工程系統、倉庫物流系統;直到上層的探索式資料分析、可視化、警報系統。在工業物聯網的OT端,將更著重資訊即時性,才能及時示警、告知事故;進而執行長期狀態監測、預診故障,以便讓OT人員提前解決與維護。至於在IT端執行的品質、物流管控及接單生產資訊,也必須與OT端緊密融合,找出最佳自動化平台來整合資訊,落實數位轉型的智慧製造,使之供應鏈能即時回應對策。
依台達分析目前產業推動智能化的第一步,即應該先實現工廠數位可視化,導入相關技術應用以洞悉生產管理,並加速邁向智能製造,對應不同製程和產業需求,建置各自所需技術連結;透過收發數據來瞭解不會說話的機台現狀,實現設備的可視化溝通。強調智能工廠管理趨勢的重點,便是數位轉型、資料及數據導向;完善管理則包含數據蒐集、分析和保存,做好數據來源控管。畢竟產線調度和生產決策都來自於主管的人,才能在進入AIoT大數據時代之後,作為支持決策,提升產線效能的依據。
為此提出的設備自動化整合控制平台DIAAuto介於OT/IT之間,可藉此負責智能自動化生產/運搬設備,與DIAWorks製程營運管理系統(MES)之間資料轉換;並透過SCADA實現可視化要求,執行整廠(線)設備管控與物流搬送工作。接著向上串連更大面向應用的製造營運管理系統DIAWorks,整合包含製造執行系統MES、品質管理系統SPC、設備工程及工廠物流的倉儲管理系統WMS,即時洞悉與排查製程異常,以提升生產品質。
目前台達已利用其洞悉市場並發揮自身產線智能升級所累積的豐碩經驗,與完整工控產品布局優勢,由下至上陸續貫穿OT層、邊緣層與IT層,依序整合智能產品、智能產線與智能工廠,由點、線至面發展出整合多套自動化系統、具「立體維度」的智能製造解決方案。
其中邊緣層係透過DIABCS整線設備管控與DIAEAP設備自動化控制兩套系統和設備互動及進行資料處理與轉換,不僅在發生異常時可以下達命令停機,更可透過系統運算分析轉換有用的洞見,提供上層系統「即取即用」,降低工作負載。IT層對應的營運管理系統也可視企業需求建置品質、設備、製程配方管理、倉儲物流等功能模組,貼近實際使用需求。
除了通過設備連網自動化控制系統DIAEAP、可視化工業圖控軟體解決方案VTscada,結合機聯網將數據依序傳輸到SCADA、品質管制統計製程管制系統DIASPC,再反饋資訊到MES二次分析;同時利用機聯網來篩選、掌握關鍵要素,例如溫度、水流、氣壓、電流,以及分析實驗室參數來產出報表和趨勢分析圖,打破以往孤島架構。
既可經由Gateway統整、串聯MES、SPC系統;以溫控器和酸鹼值計搭配HMI、PLC,控管各區溫度與酸鹼值,即時擷取溫度、流量、PH值、壓力、水阻值及實驗分析數據等。藉此結合IT+OT優勢,提供更高效品質管理決策判斷;即時反饋資訊,加速人員追溯原因,快速盤查應變措施及恢復運作。。
台達認為,目前業界執行可視化監測目的,係為了因應工業智能化趨勢,掌握全場數據。於底層透過機台端感測器蒐集而來的設備運作訊號及數據,經擷取原始資料動態特徵值,優化設備運作和產線效率;再經過數據運算應用AI+ML,將實際需要監測數據,自行設立門檻管理;最終由系統/使用者掌握各種製程參數,將物理量透過運算轉換為實際監測項目,輔助分析執行最佳決策。
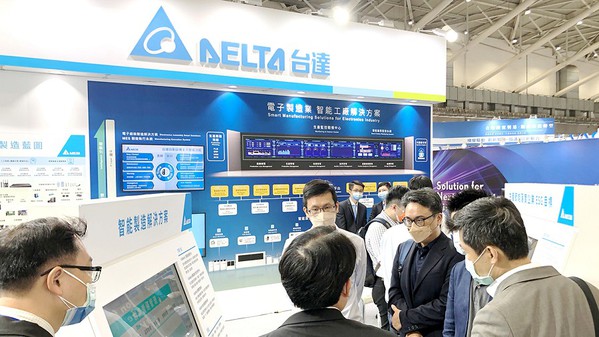
圖2 : 目前台達已利用其洞悉市場並發揮自身產線智能升級所累積的豐碩經驗,與完整工控產品布局優勢,由下至上陸續貫穿OT層、邊緣層與IT層,依序整合智能產品、智能產線與智能工廠,發展出智能製造解決方案。(source:台達電) |
|
洛克威爾推出Edge Getway新品 加速實現Low/No code應用
美商洛克威爾自動化公司(Rockwell Automation),則在上世紀90年代後期逐步開發PLC硬、軟體整合的自動化控制平台Logix,能同時處理離散、流程、運動、安全、機器人等多種策略控制任務,並持續拓展在AI+IIoT領域發展,共分為ControlLogix、CompactLogix不同層級。
當時推出的FactoryTalk Analytics LogixAI分析模組,就是基於 ControlLogix平台的FactoryTalk Analytics系列產品最新成員,既可用於了解自動化系統的架構,並向產線人員指出各個設備問題。再將FactoryTalk分析和機器學習技術嵌入到Logix的控制環境中,能在沒有資料科學家協助的情況下,為其自動化系統賦予了可針對生產流程中的操作變數、異常狀況,進行預測性分析的能力。
由於該模組係透過外掛於ControlLogix控制器的應用分析程式來改變規則,以實現流程改善,所以可直接安裝在控制機箱中,經由背板串流控制器同步進行高速資料傳輸資料,擴展了對於運行資料採集存儲、運算分析和挖掘處理的能力;進而構建預測模型,連續監控製造營運、偵測異常,使操作人員能輕鬆應用機器學習概念,來解決產品品質問題;同時協助保護過程完整性,毋須開發、驗證或維護自製的機器學習演算法。
另針對異常偵測和軟測量(Soft Sensor)建立AI建模引擎,使得LogixAI模組可利用AI來檢測、判別生產異常情況,進一步擴充系統功能。讓產線OT人員可更輕鬆分析、使用其設備中的資料,來預測生產問題。包括開箱即用異常偵測,使客戶能在偏離設定點之前採取行動;用於軟測量時,可在無法部署感測器、儀表的環境下,代替人工讀數來預測操作值。
進而透過人機介面(HMI)或儀表板的警報,發現可能影響產品品質或導致停機的效能偏差,以便於必要時調查或介入解決問題;或經過這些模組持續進化,結合最新自動化控制技術,來實現製程的最佳化。客戶藉此都能從改善高品質產出、提高資產利用率,以及在其智慧營運旅程的特定學習經驗中調整而獲益。
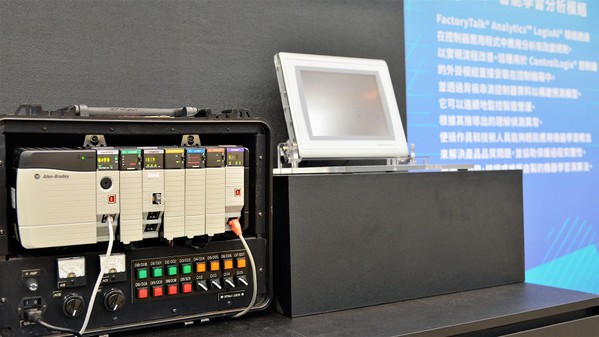
圖3 : 洛克威爾公司推出LogixAI模組,透過外掛於ControlLogix控制器的應用分析程式來改變規則,以實現流程改善(攝影:陳念舜) |
|
此外,回顧過去20多年的Logix發展史,其投入技術的重點主要在於解決自動化系統運行過程中,與控制相關的各類問題。但在遭遇要對系統運行資料進行存儲和分析任務時,以往Logix都會通過網路通訊埠EtherNet/IP,交由上層資訊化平台FactoryTalk Analytics for Device進行分析處理。
但隨著資訊化與數位化在製造領域促成IT與OT深度融合,使用者開始希望自動化系統能在控制層,開始針對系統運行資料進行分析和處理。藉以減省部署和營運IT系統的成本、分擔資訊化平台的運轉負荷,符合資料運算與處理的即時性要求;對於資料的當地語系化處理,而提升系統的資訊安全。「對於部署工業物聯網技術的企業而言,如今在雲端和現場(地端)架構之間,同步進行作業已不可或缺。」
直到這兩年來製造業開始浮現對於自動化控制系統的資料分析型應用需求,卻難以找到可同時具備此類軟體發展與交付能力的使用者與服務商,從而催生了FactoryTalk Analytics LogixAI模組。
除了硬體方面與上一代工業電腦運算模組產品相同,都可插接於ControlLogix 5480控制器機架上,同步進行高速資料傳輸資料,擴展了對於運行資料採集存儲、運算分析和挖掘處理的能力。且因為CompactLogix控制器具有在本機上運行 Windows應用程式的能力,可將Logix控制引擎與 Microsoft Windows 10 IoT Enterprise作業系統集中於同一平台,便於工作人員在資訊來源處查看機器資訊,避免單獨使用PC而縮減機器的占地空間。
如今,LogixAI模組不僅更名為FactoryTalk Analytics系列,且預置內嵌了相應的軟體應用程式,讓使用者不用像過去須加裝基於Windows/Linux OS的各類單獨應用程式,就能直接通過乙太網埠接入模組。使控制器能在機器層級存取控制系統資料,即時收集原始機器資料減少時延;並從雲端獲取深度資訊,將資料以有用資訊的形式提供給工作人員,得以更好應對各類問題,提高生產力。同時發送其他資訊到上游的企業或雲端,降低了系統對於PC或雲端網路等IT資訊化設備的仰賴,還有助於減少記錄資料的時間延遲,進而讓企業用戶可從源頭即時查看控制資訊,更快速敏捷地作出明智的營運決策。
在Web瀏覽器上針對相關應用模型進行參數配置,即可對於控制系統的運行資料進行分析,和預測可能出現的異常狀況,被官方稱為嵌入式分析(Embedded Analytics)。不僅降低了系統對於PC或雲端網路等IT資訊化設備的仰賴,還有助於減少記錄資料的時間延遲,讓用戶可從源頭即時查看控制資訊;同時可將其他資訊發送到上游的企業或雲端,讓工作人員能夠更好地應對各類問題,最終提高生產力。
藉此為使用者省下了原本從取得資料到分析處理過程中,須大量耗時和成本,投入發展與部署應用軟體的工程,為其預測性應用提供了一套標準自動化資料分析的套裝軟體。此也突顯了內部所整合的應用模型選項和預測分析演算法重要性,目前LogixAI的演算法和自學習模型主要源於FactoryTalk分析軟體,未來應該也會根據使用者需求,持續進行深度學習與和反覆運算。
台灣洛克威爾國際公司自動化產品技術顧問高永勳指出,目前LogixAI模組也新增了可用歷史建模功能,有助於透過背板直接擷取PLC的Real time資料建模,在設備生產同時蒐集資料與修建模型,得以提供LogixAI模組上萬筆資料直接建模,應用範圍更廣。幾乎可被視為小型AI控制器,不僅能直接控制實體驅動器、馬達動作;只要通訊協定相容,甚至可搭配任何品牌PLC成為外掛Edge AI電腦,直接從LogixAI模組自主撈取資料而降低門檻,可在客戶編程同時,自行訓練企業級中小規模AI模型且兼顧資安。
此可歸功於PLC內建參數,而不必像過去智能化控制必須重頭開始編程,將設備控制資料上傳控制器或PC,與IT分析模型資料區隔。現在只要透過洛克威爾最新推出的Edge Gateway軟體,即可自主蒐集PLC內建real time資訊,包括I/O、CPU狀態等資料並結構化,再透過PLC背板以10ms高速傳輸到Logix AI模組,進行分析與可視化,更直覺反應現場異常狀況,提升可靠度。
高永勳認為:「與過去最大不同的是,現今PLC編程工程師已不再被認為最了解製程者,許多負責訓練資料分析模型者撈取到的,並非傳統工程師認定最重要的資料,所以會將PLC內建所有參數都上傳到Edge端,再自動經過通訊掃描所有PLC,找出須要分析的異常模型。」藉此因應現今許多生產流程的問題,不只發生在馬達硬體、警示燈號,而可能是在通訊網路上,進而找出網路記憶體、CPU即時狀態,選擇是根據設備異常或產線資料,直接在Edge Gateway蒐集遠距I/O、CPU資料建立模型分析,而不必再編程。
並分為可針對生產過程中設備參數,直接在PLC分析處理資料的LogixAI模組;或再交由上位Edge Gateway蒐集更龐大資料分析時,預設PLC使用率或警示等參數,得以更方便建模;Edge Gateway也能直接擷取IO link感測器、變頻器等智慧裝置資訊加以分析,或是自主判斷光電開關的紅外線光源是否衰減,進而示警、排除鏡頭髒污。
希望除了賦予PLC更多智慧化功能之外,還能提供更多已結構化資料,不必再編程時間,而可以快速擷取、分析及跑AI模型,已越來越接近PC-Based控制器已內建CPU、記憶體使用率及I/O狀態、網路監控等資料分析內容,且更為可靠、穩定。亦可借助LogixAI模組及上位Edge Gateway來分攤PLC工作量建模,與更多平台及軟體相容且符合資安規範,可歸功於PLC內建參數,此也皆符合ISA-95規範,讓使用者不必將時間浪費在蒐集、整理資料上,從而直接進行分析,並進行Low/No code應用。
結語
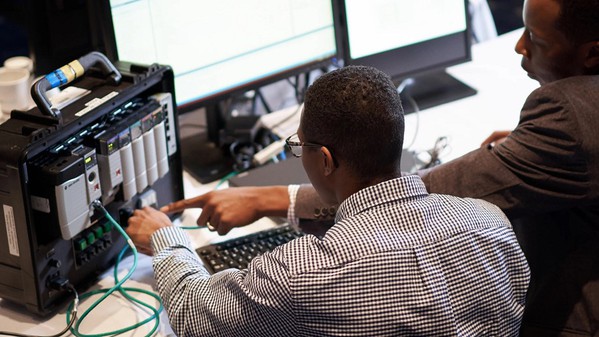
圖4 : 如今業界可透過持續透明化、可視化來即時掌握自動化設備的更新和優化製程,同時加強數據應用能力以優化及支援決策。(source:rockwellautomation.com) |
|
值得一提的是,回顧過去因為台灣中小企業普遍面臨缺工及資深員工占比高、對數據敏感度低,即使台灣在工業2.0~3.0時代曾由如永彰科技公司1989年引進日立、攝陽之於三菱電機等品牌FA(Factory Automation)經銷商通路導入自動化解決方案,開始建構數位化資訊環境,卻仍因員工基礎知識不足而難以導入,老師傅仰賴過去經驗決策,導致在判斷和邏輯上耗時與成本。
如今則可透過持續透明化、可視化來即時掌握自動化設備的更新和優化製程,同時加強數據應用能力以優化及支援決策。包括透過PLC對話流程來掌握數據,提高製程效率與可靠度;整合越來越多,推陳出新的進階監控方法,以涵括不同廠區設備的長時間運作和傳送數據,並及時發送警報;最終利用聯網普及來實現智慧工廠,借助數位轉型達成產線自動化,達到工廠管理與控制最佳化。