根據近年來無論是Boeing、Airbus發佈的最新市場調查報告,均評估未來20年全球商用客機市場將達到35,000~40,000架。且為了提高現有機體、引擎生產效率4~5倍,兼顧穩定品質、降低成本,投入智慧製造也成為台灣航太產業鏈的必經之路。促使有意搶奪這波航太製造商機的台灣工具機廠商,紛紛導入國內外解決方案,以求改善產品與製程。
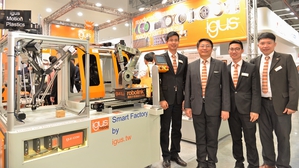 |
易格斯公司(igus)是現今唯一開發可線上配置,和預測拖鏈使用壽命的供應商。 |
如台灣工具機製造廠協鴻公司在50年的歷史中,分別向65個不同國家出口超過46,000台機器。且自2017年以來,就不斷開發AERO系列的CNC設備,用於製造航空工業所需大型零件的機器人加工中心,精度和可靠性尤其是關鍵因素。
因此,使得從工具機電控箱到主軸、馬達等可靠供能方式變得非常重要,並要求所有軸向位置和移動的資訊須不間斷回傳控制系統,使得該系列首款機型的加速度可高達0.5G、最大行程速度約60m/min。
且由於工具機製造商通常會避免在系統上同時執行太多不同的工作步驟,以降低出錯的可能性,必須選擇來自單一供應商的可靠性完整解決方案。易格斯公司(igus)則是現今唯一開發可線上配置,和預測拖鏈使用壽命的供應商,並專門設計chainflex耐彎曲電纜,每年在占地2,750平方公尺的測試實驗室中進行20億次測試。
目前該公司全裝配拖鏈可在全球12個生產設施訂製,再將此即裝即用的產品交付給客戶,在其加工中心機內採用igus全裝配拖鏈系統,為製造廠商有效精簡流程步驟,可將裝配時間從幾周減少到半天;還能節省流程成本或避免出錯,提升競爭力。
針對協鴻的AERO系列設備所提供的客製化解決方案,係透過igus拖鏈可顯著減少所需安裝空間;並在機器上所有chainflex耐彎曲電纜都搭配耐油的PUR外護套,無需額外的保護軟管,得以減少空間及降低拖鏈尺寸,大幅降低成本及簡化保養;進而創建出帶有裝配框架的裝配拖鏈3D圖檔,以模擬裝配過程,僅約1hr內就將所有配備電纜的拖鏈安裝於機器上、附帶油管的第二條液壓軟管拖鏈僅需40mins。
有別於以往需要2名員工用1周半時間在AERO系統的X軸上工作,再花費1周時間在Y軸和Z軸上安裝供能系統。經過採用igus全裝配拖鏈後,即可於半天內安裝完畢4個拖鏈,讓協鴻能有效精簡工作步驟,降低流程成本並提高生產率。