工业4.0是近年所有制造业皆在努力实践的目标,麦肯锡(McKinsey)去年针对欧、美、日等地的制造大厂进行调查,根据调查显示,在这些推行工业4.0的企业当中,仅有四成认为有获得成效或在改善制造流程中取得良好进展,这个结果虽然不至於太惨,但也算不上取得好成绩。而观察台湾市场,半导体大厂英特尔则认为,由於制造业族群分布零散,不同产业在落实工业4.0中,从技术成熟度、策略方针到问题痛点等都具有很大的差异化。企业在实践工业4.0的第一步,应当先审视自己所处的位置,以找出最合适的解决方案。
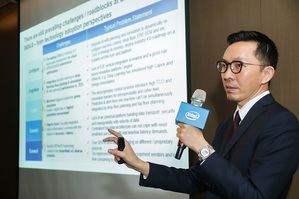 |
英特尔亚太区制造业产业解决方案总监李立仁表示,英特尔期??协助台湾企业於工业4.0浪潮下,精准转型智慧制造。 |
英特尔亚太区制造业产业解决方案总监李立仁表示,不同族群在工业4.0所使用的技术成熟度来说有很大的差异,例如传产可能连第一步将设备连网的阶段可能都还未达到,可遑论现今炙手可热的人工智慧等。但有的产业却已经在深入研究如何运用AI、机器学习等技术,让设备自主优化。李立仁近一步观察,其中,又以半导体和面板业在技术上较为领先。
那麽企业如何审视自己究竟达到工业2.0还是3.0呢?李立仁表示,企业可透过讯息物理系统(Cyber Physics System)当中的5C架构来进行评判标准,他认为,此5C标准非常适合用来检视工业4.0技术的成熟度,并辅助企业审视各阶段所需的代表性能力与技术。
5C架构从最底层初阶技术至最高层高阶应用共可分为五个能力组成,分别是连结(Connect)、转化(Covert)、虚拟(Cyber)、认知(Configure)以及自我配置(Configure)。进一步说明,最基本的连结,在这阶段最主要的就是将OT与IT进行整合,透过物联网技术让机器与机器间能够互相通讯、进行串联。
其次,在转化的阶段中,则是让设备机台在初步的连网後,将撷取到的资讯转换为具有分析价值的数据资讯,例如设备的失效或良率的分析。其中,设备端点须具备分析、智能化的能力是这一阶段中非常关键的能力。在第三个阶段虚拟中,则是强调虚拟化的数位工厂(Digital Twins),在所以机台都连网之後,形成另外一个虚拟、同步化的工厂运行,而其数位工厂具备感知、预测能力,可预测「非计画内」的设备故障,当故障讯息被数位工厂撷取後,更可以模拟接下来如何执行最隹化的重新排程。李立仁也举例,像日本近年就非常致力於推动数位工厂的运行。
至於第四层认知,在这个阶段主要则是导入如机器学习、深度学习等一系列的人工智慧技术,让机器可自我学习、进化,并从大数据分析中不断进行推算与模拟,进而在设备端预防机器故障与良率不隹的状况。
最後一个阶段自我配置,则是能够机器能够藉由感知、学习的结果,以自主的方式改变机器设备的设定,就好比自动驾驶的概念,利用系统对环境变化的判断与分析自动更改执行命令。而工厂的机器同样也能够根据感测系统、订单需求等的变化重新排程,订立最隹化的结果,这也是目前工业4.0追求的最高层级。